Features応原工業の複合材料の
試作・圧縮成形プレス金型製作の特徴
特徴1創業50年以上
金型設計・製作の
高い技術力
当社は、創業以来50年以上、自動車部品の樹脂プレス金型の設計・製作を行ってまいりました。長年培ってきた技術力への評価をいただいており、本社のある広島県のみならず、全国各地のお客様と取引をさせていただています。
この技術で、複合材料の金型も高精度に加工し、複合材料の試作を行います。万が一、製品に不具合が発生した場合でも、金型から対応しているため、すぐに解決いたします。
また、当社の複合材料成形システムは、カスケード制御により、形状面に近い箇所も温度管理しています。これにより、適正な成形温度を維持でき、理想的な成形条件にすることが可能です。
当社では、これまでプレス成形では難しかった複雑形状やリブ形状、また複数の材料を同時に成形することで製品物性・温度・重量・コスト・形状やデザインといったお客様の課題解決をご支援します。
特徴2数個程度の試作から対応
ロットに応じた
コストダウンも可能
当社では、数個程度~数百個程度までの複合材料の成形が対応可能です。
また、金型に関する長年の知見を活かし、通常プラスチック金型で使用されるハイグレードなプリハードン鋼、一般的な炭素鋼、鋼材費を削減できる鋳鉄など、樹脂の種類や使用頻度による耐久性・要求品質に応じて最適な金型の鋼材を選定することでコストの最適化を実現します。
特徴3他社では対応できない
大型サイズの複合材料用金型の製作及び
試作トライが可能
当社では「熱硬化性樹脂向けの熱成形」・「熱可塑性樹脂向けの冷却成形」だけではなく、「ヒート&クール成形」が可能です。
成形可能な温度は5℃~400℃です。
当社では1,000×1,200サイズの冷却ベースに加え、1,300×1,800サイズの冷却べ―スを保有しており、複合材料成形システムを用いた場合、最大金型サイズ 1,000×1,500 までの製作及び試作トライが可能です。小型のワークだけでなく、他社では対応できない大型サイズのワークにも対応が可能です。
*条件により1,300×1,500サイズや1,000×1,800サイズの大型金型の製作及び試作トライも可能です。
*プレス機のベットサイズは1,600×2,600なので、冷却べ―スを度外視すればさらに大型の金型も可能です。
特徴4熱硬化性樹脂の成形なら最大型サイズ
1,550×2,000 まで対応可能
当社では自動車内装用金型を手掛けておりますので、既存設備を活用すると型サイズ1,550×2,000 まで対応が可能です。
その場合ヒート&クールはできませんが、成形温度は 260℃まで対応可能です。
主に自動車業界向けの実績が多数ございます。
大型の熱硬化性樹脂をマトリクスとした複合材料の成形をお考えでしたらご相談ください。
特徴5製品サイズに応じた
材料をアレンジ
500までのプリプレグ、
板材の成形が可能
従来は、複合材料を購入するとなると、大板で購入する必要があったため、製品サイズに比べて大きい場合が多く、コスト増につながっていました。
また、材料メーカーの規格品がなければ、連続繊維/プリプレグ(樹脂があらかじめ予備含侵された炭素繊維シート)を用意することができませんでした。
当社ではプリプレグ成形用金型を内製しているため、連続繊維/プリプレグのVF率調整も可能です。
また、材料厚みは20tまでの板材が成形可能で、UD材・チョップ材・不織布などを組み合わせることでお好みのプリプレグや板材の製作が可能です。
特徴6成形材料のアレンジや、
リサイクル材に対応
当社では、成形材料のアレンジも対応可能です。材料に応じた最適な金型製作・製品試作を行います。
また、一般的に複合材料はリサイクルが難しいと言われていますが、最近は技術開発が進み、新品よりも価格の低いリサイクル材もあります。
環境にも優しいため、多くのご相談をいただいております。
お気軽にお問い合わせください。

Works製品事例
ドローンアーム(ハット形状・リブ形状)
材質:UD 材+チョップ材 / クロス材+チョップ材 / 不織布材+チョップ 材 / 不織布材 / チョップ材
ドローンは長時間・長距離を飛ぶ必要があり、荷物や農薬などを運ぶために軽量化が求められます。そのためドローン部品には、金属より軽く、金属相当の強度のあるCFRP複合材料がよく使われます。
こちらのワークは、先端の穴にブレード(羽)を取り付けるドローンアームの試作品です。
表側はクビレ形状と製品の高低差があるため、成形性と温度管理が難しいワークです。
裏側は強度を持たせるためのリブのイメージと、ハチの巣形状で金属では成形できない形状を表現しています。
成形方法はプレス成形で1ショットで成形しました。
ドローンブレード(回転翼)
材質:クロス材+発砲材+心材
こちらは当社の試作金型で成形した、全長は350mm程度の片翼仕様のドローンブレードです。
想定しているブレード(回転翼)は1機あたり1セット2枚×4カ所で計8枚のブレー ド(回転翼)が必要なイメージです。
ドローンブレードは回転することで浮力を発生させ、ドローンの機体本体や農薬、荷物などの積載物を運搬する必要があるため、他のドローン部品同様に軽量化と強度が求められます。
今回の試作では発砲材をクロス材で包むように成形し、強度が必要な部分に心材を使用しました。
複合材料の種類は熱硬・熱可塑を問わず、発泡材、コア材、最外層の表皮などの材料を最適に組合わせることでドローンブレードの機能を表現できる形状となっています。
EVのバッテリーカバー部品
材質:マイカ
こちらは、EVのバッテリーカバー部品です。
ある材料メーカーから自動車部品に参入したいとのことでご相談をいただき、金型を製作いたしました。
バッテリーが発火しないように、「マイカ」という絶縁性の材質を使用しています。まず試作型を製作し材料や成形条件の検証を進め、その後すぐに本型を製作するに至りました。
今回のケースでは、試作型の製作開始から約1年で量産に至りました。
自動車エンジンルームの補強部品(リブ形状)
材質:UD材+チョップ材 / チョップ材
自動車のエンジンルーム内の板金部品を CFRP に置き換えた 1/2 イメージの部品です。
現在の自動車のトレンドである EV 車はバッテリー重量が重いため、車体重量が内燃機関の車に比べて重くなりますが、部品の素材を金属から CFRP に変更することで車体重量の軽量化が可能になります。
こちらの部品は製品形状をあえて複雑化し、金属では実現できないリブ構造にすることで部品の強度向上を実現しています。リブは 1mm で 深さは 23mm です。全て MC による切削加工です。
表側は UD 材を用いることでその繊維方向に対する強度が強くなり、それだけでは弱い方向や捻り方向の強度を向上させています。
成形方法はプレス成形です。
CFRP複合材料は材料費が高額なため今回、部品を成形する前に当社の 3D プリンターで出力し、形状の現物確認を行いました。3D プリンターは成形可能サイズが A4 サイズですので 3 分割し、張り合わせることで 1/1 スケールのモデルに仕上げました。
材料特性は全く違いますが、実際の形状にすることで形状的な強さ弱さを知るヒントになります。
CFRP製自動車部品の強度剛性解析
この自動車部品ではまずリブ無し形状の金型を製作し、試作後に現物確認で強度の弱い部分に焦点を絞り、金型を改造してリブ形状追加しました。比較のためにあえてリブを設置しなかった部位もありますが、この解析結果からリブ形状で強度や剛性の向上に寄与している部分とそうでない部分が明確になりました。
また、上記の解析結果を踏まえて最適なリブ配置を再検討しました。これにより部品重量の更なる軽量化と共に、ほとんどの部位で強度や剛性といった部品として必要な機能も向上させることができる結果を得られました。
当社ではこのような強度剛性解析のアレンジも可能です。

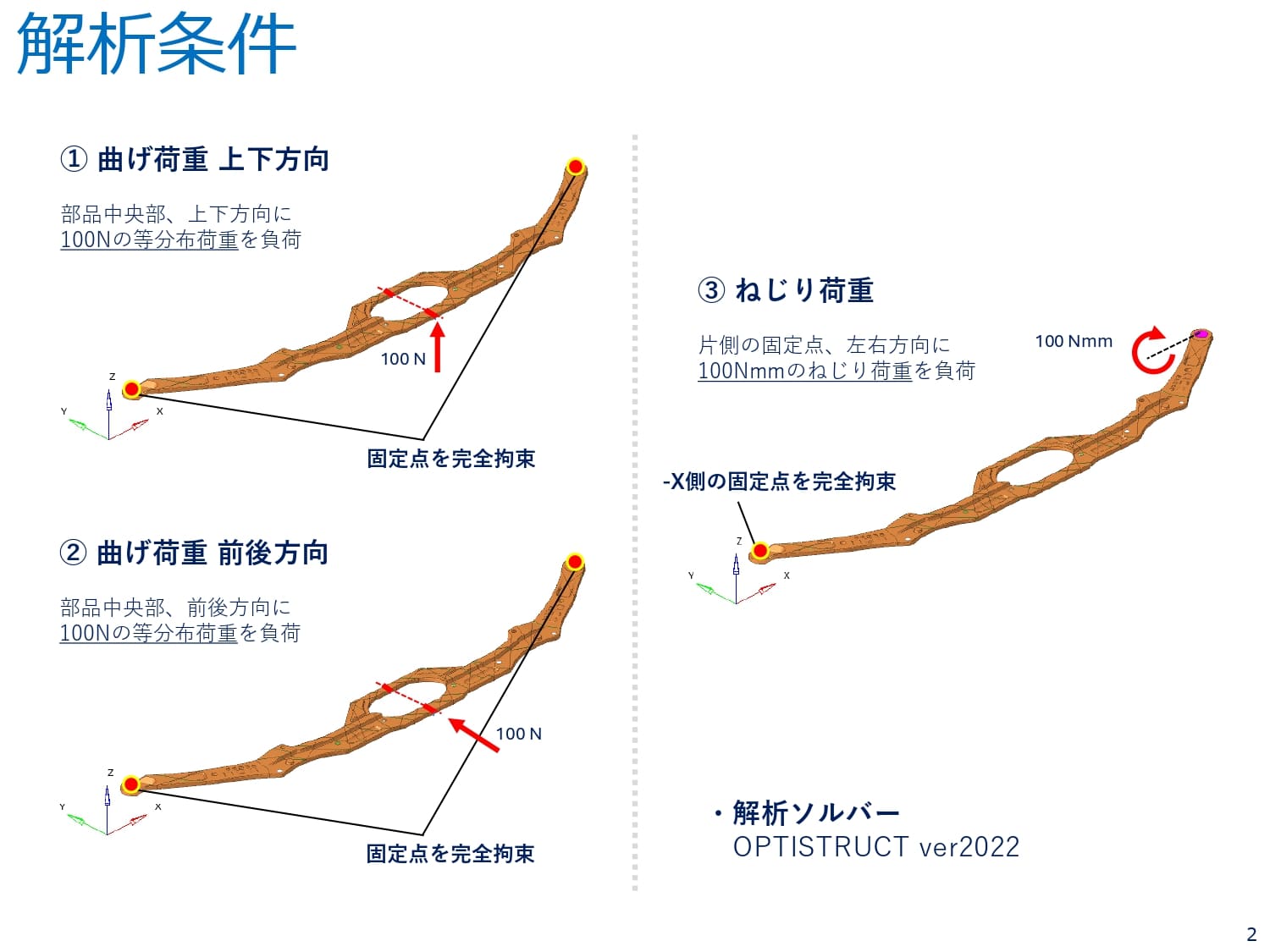
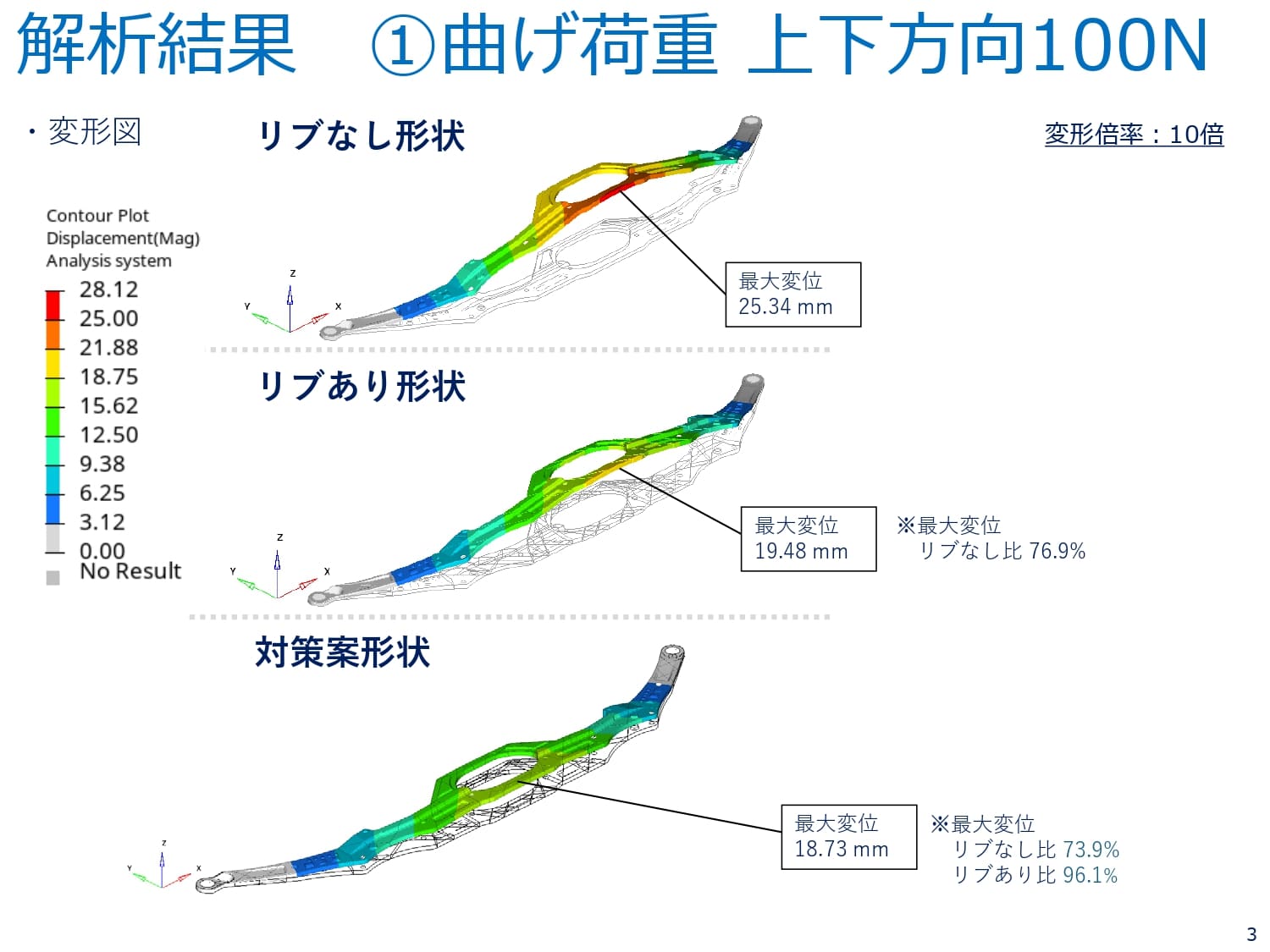
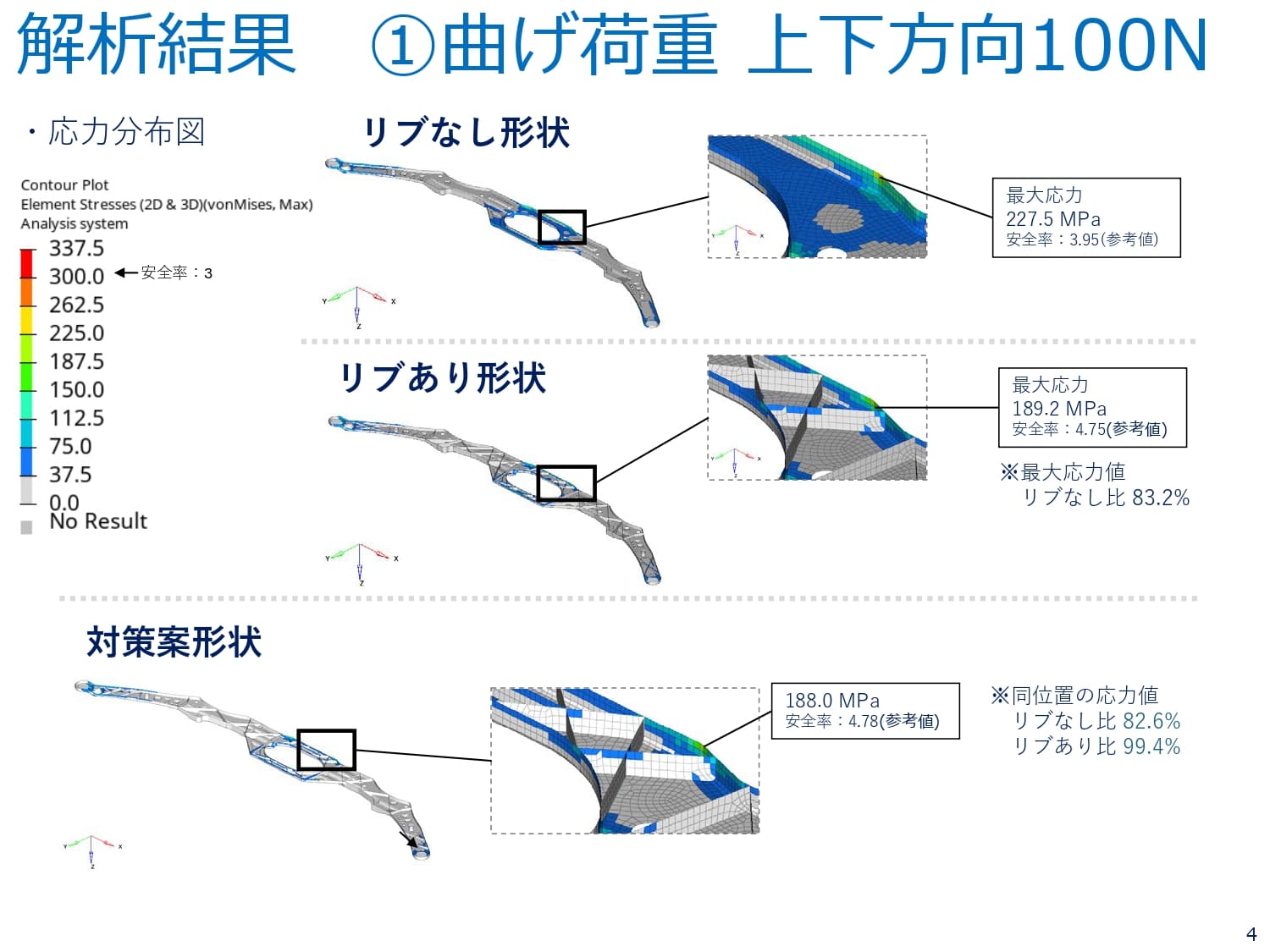
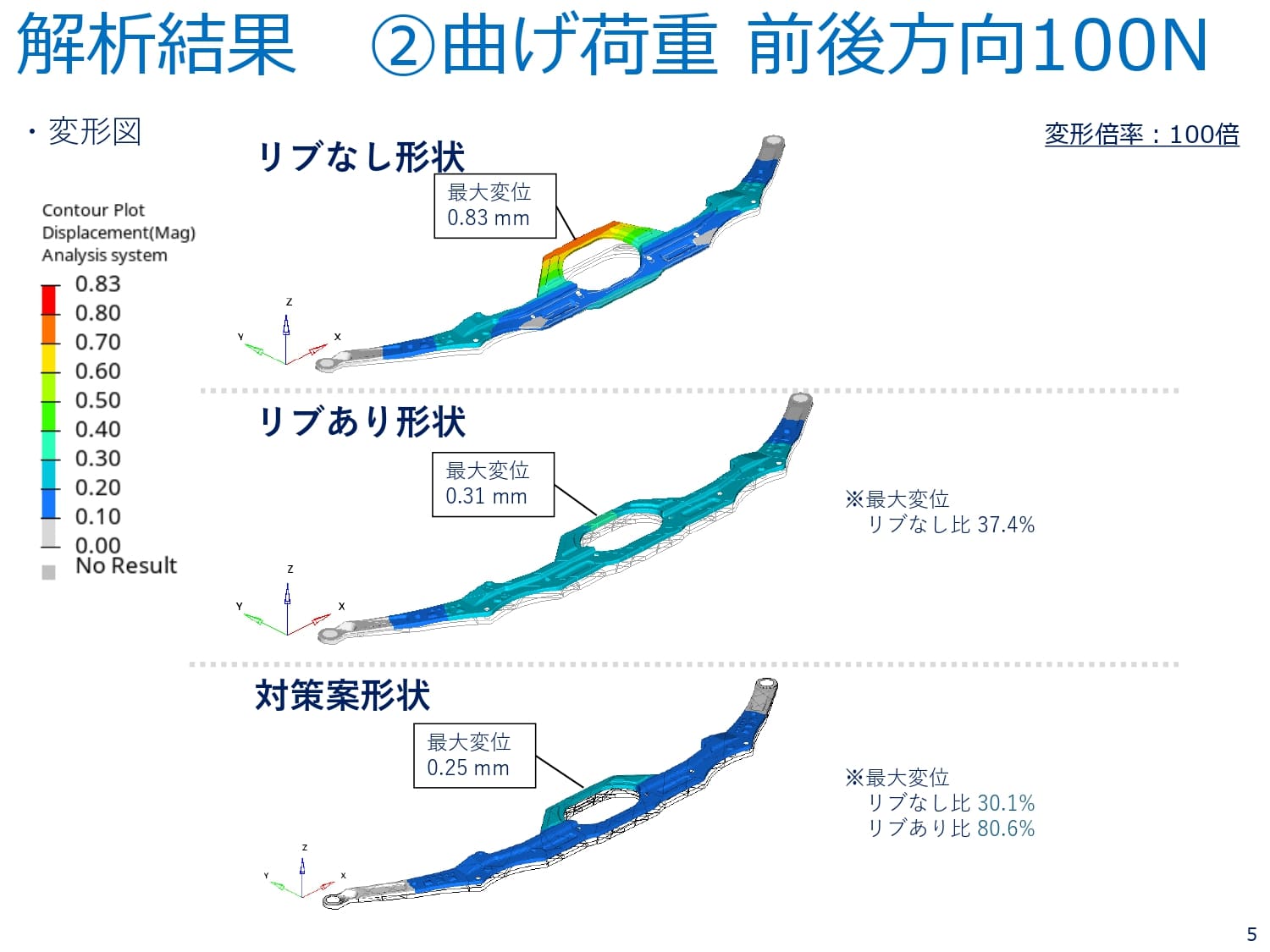
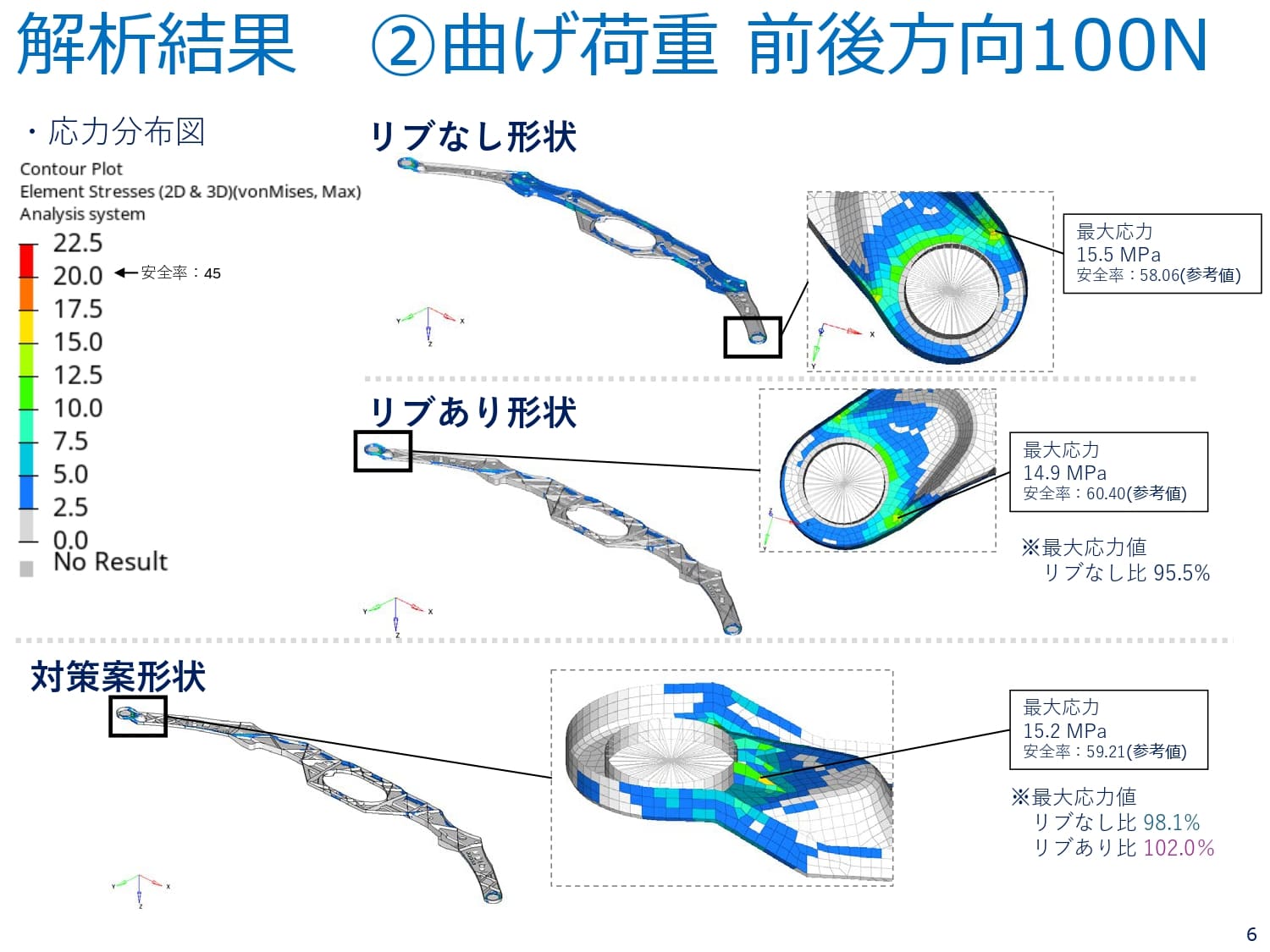
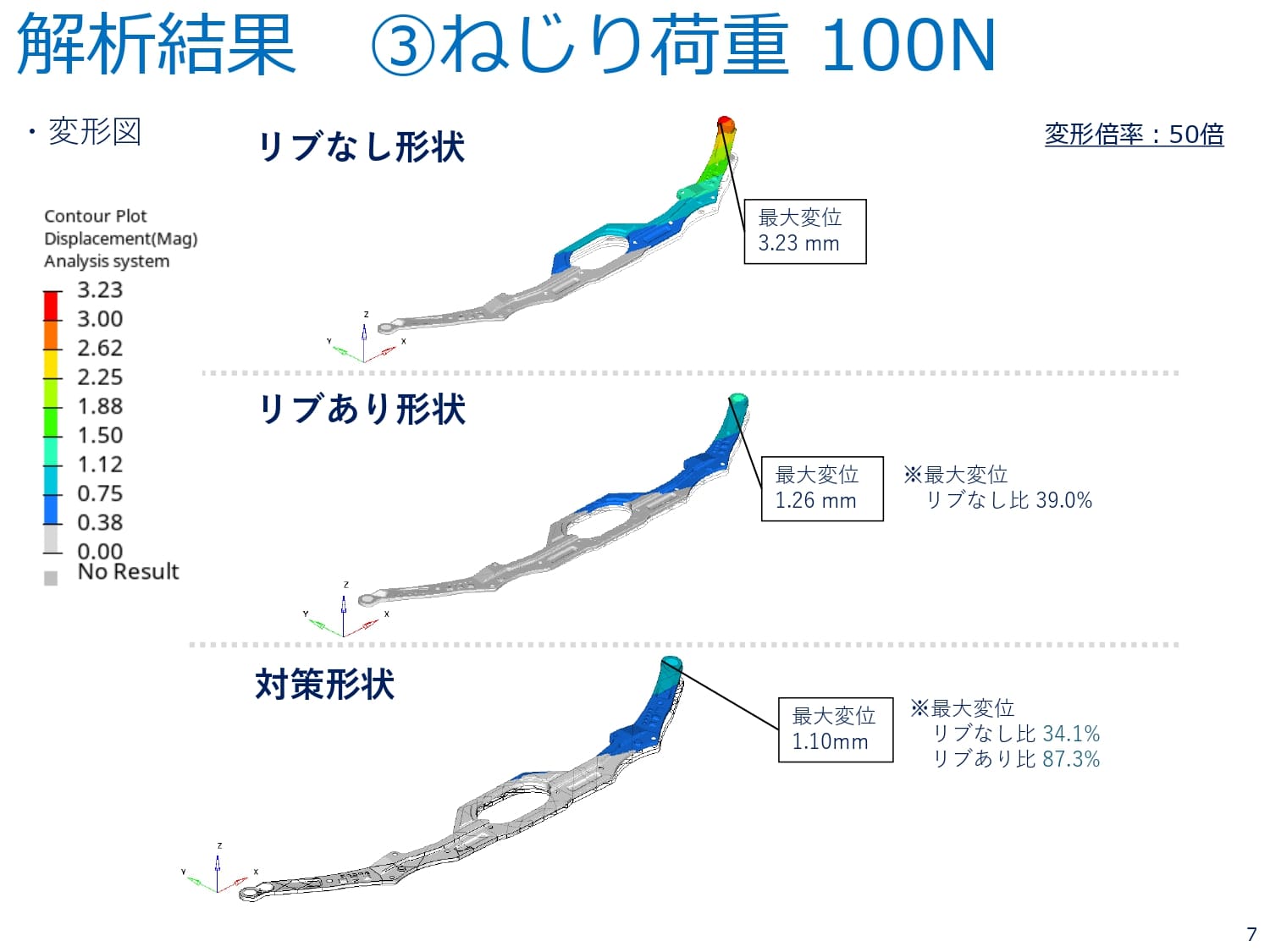
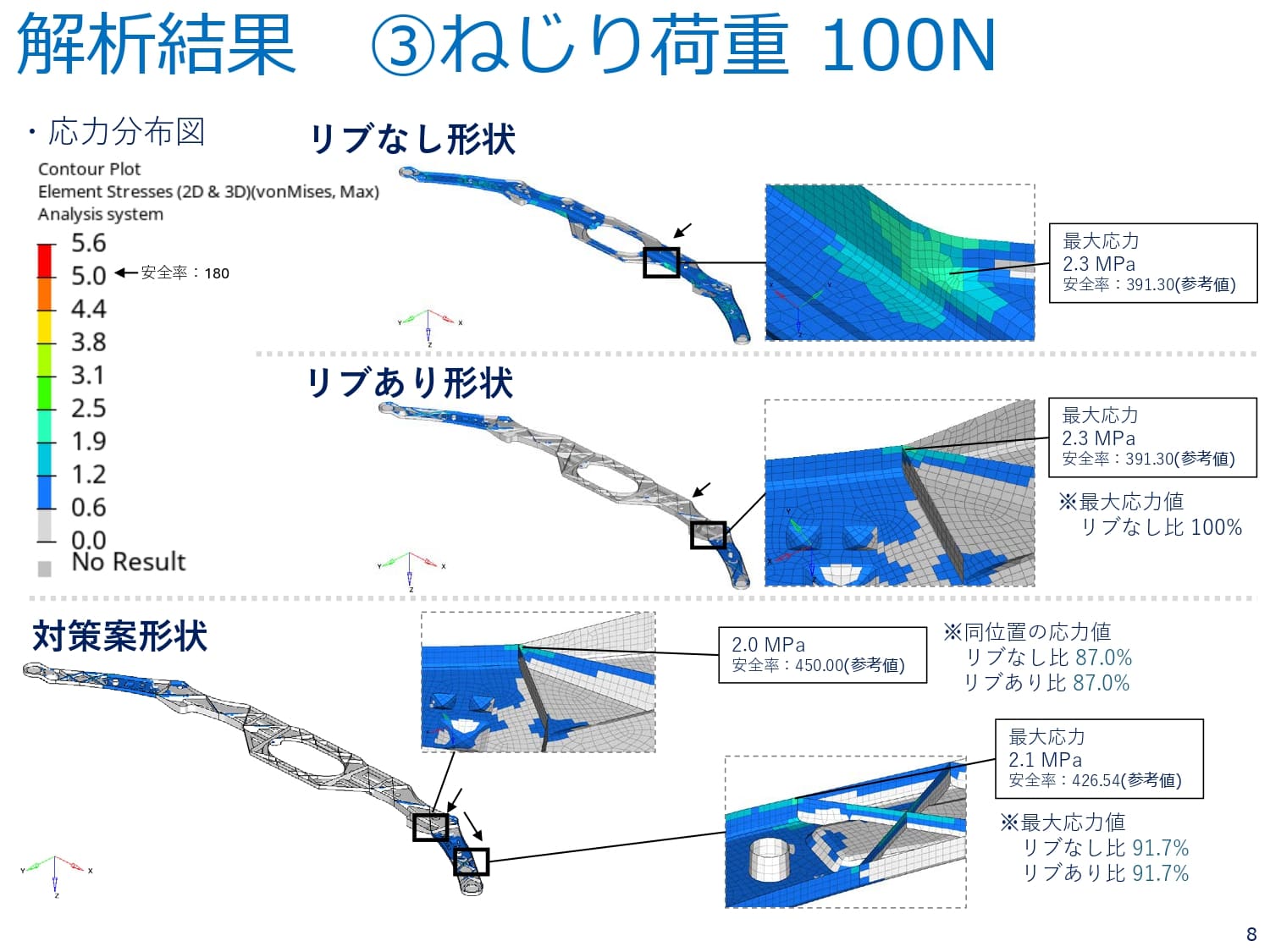
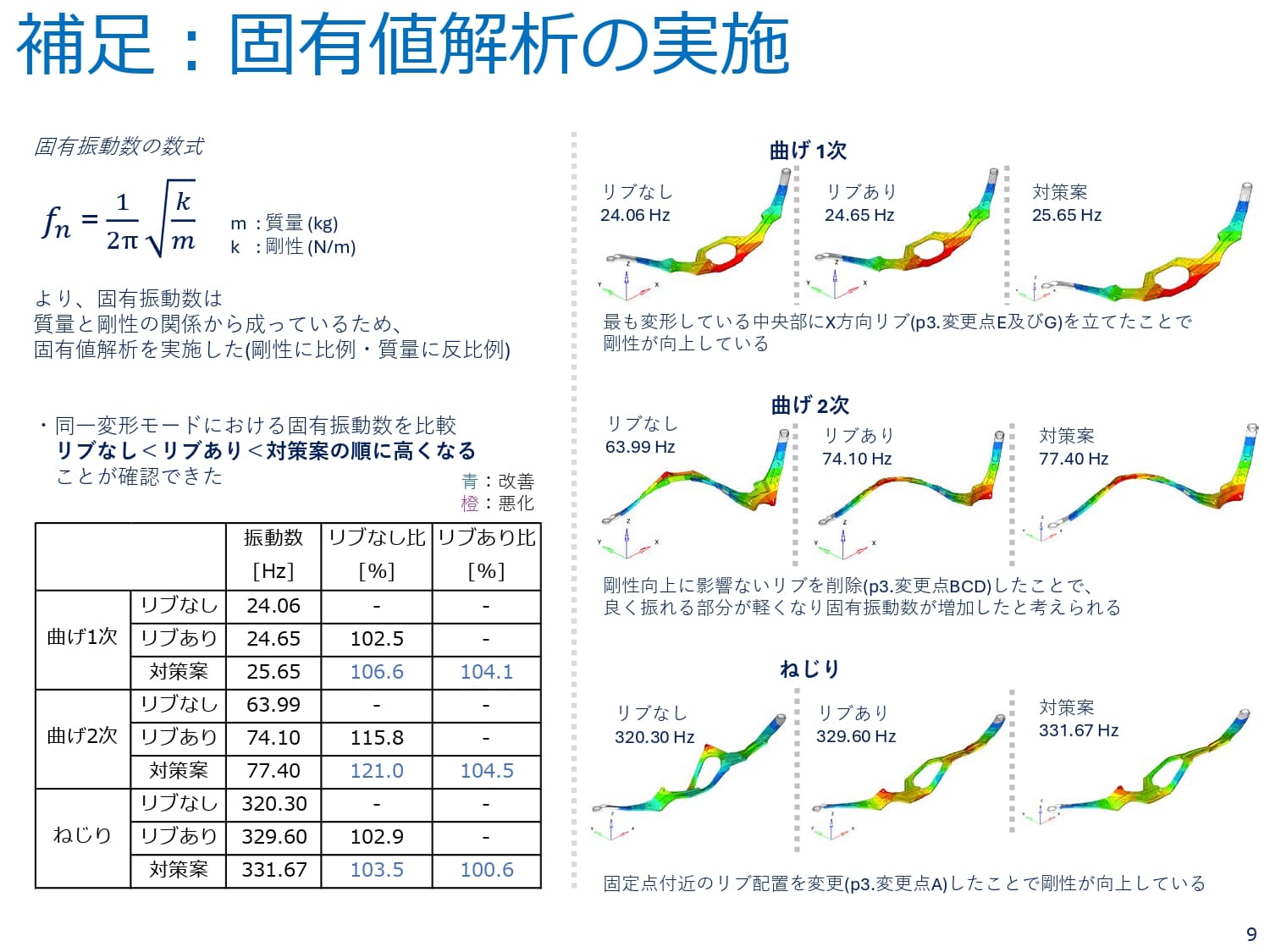
座椅子(深絞り形状)
材質:UD材+チョップ材 / チョップ材 / クロス材
床・椅子ともに使用可能な座椅子製品です。
非常に深絞り形状ですが、当社の樹脂プレス金型の製作実績を活かして金型を製作しました。
一般的な成形方法であるインジェクション(射出成型)では座椅子製品の製品肉厚4~6tほどの製品ありますが今回、CFRP複合材料の特性である軽量化と強度を活かして全面2tの製品を成形しました。
また腰の部分は「しなり」が入り、快適に座れるようになっていますが、CFRP複合材料のUD材の強度や形状剛性を持たせることで細い面での「しなり」を実現しています。
成形方法はプレス成形で1ショットで成形しました。
CFRP製座椅子の強度剛性解析
強度剛性解析を実施し、プレス生成のトライ結果と解析結果から、十分な強度を持つ製品形状を製作しました。初期形状では特に腰のくびれ部分で数箇所強度不足が見られましたが、新形状ではくびれ位置の変更と形状剛性をより深く設定することで強度を補いました。
複合材料は成形条件により成形性が大きく左右されますが、形成結果や解析結果から製品形状を再考したり最適な材料配置を行うことで課題解決が可能になります。
当社では強度剛性解析のアレンジも可能です。
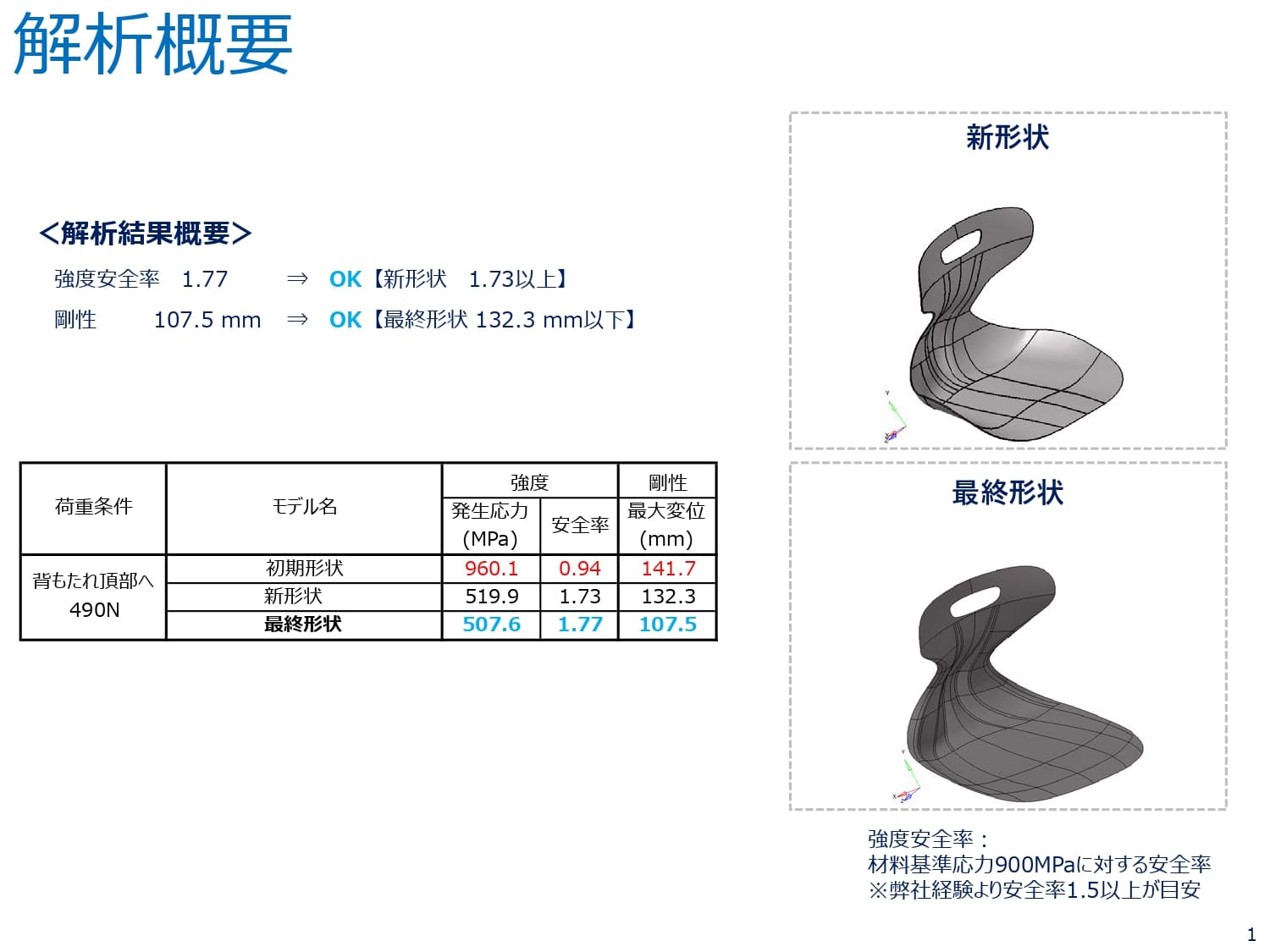
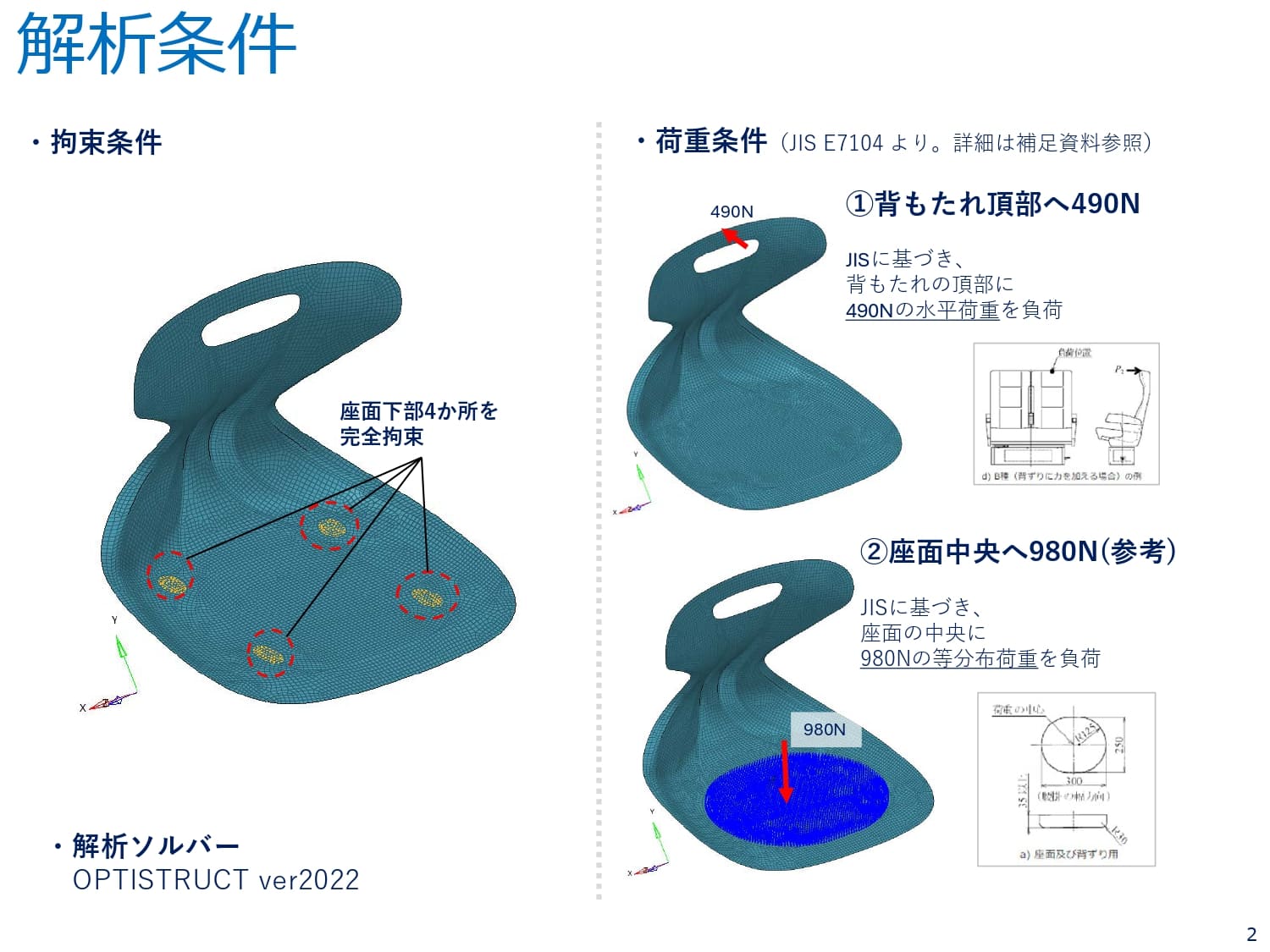
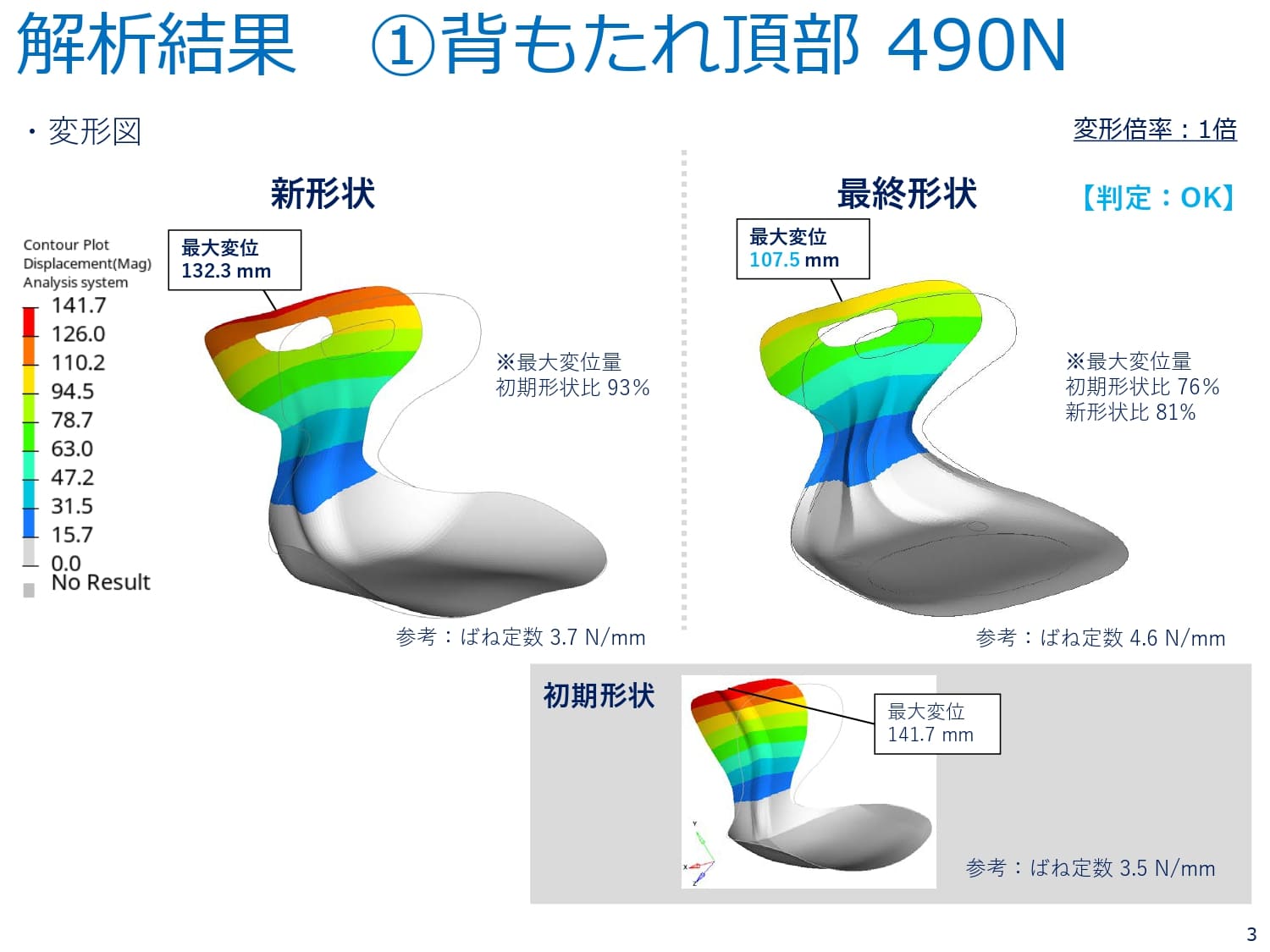
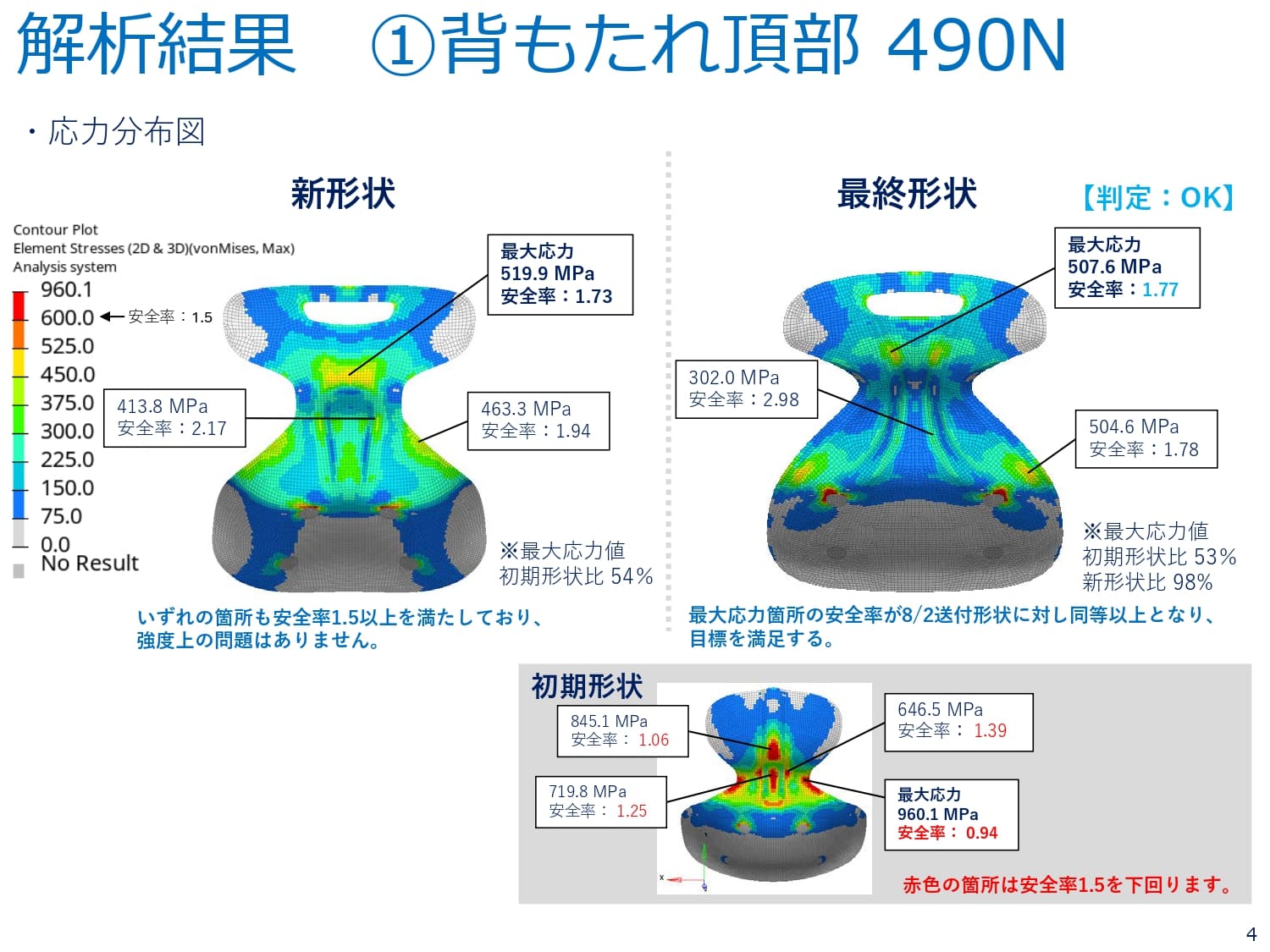
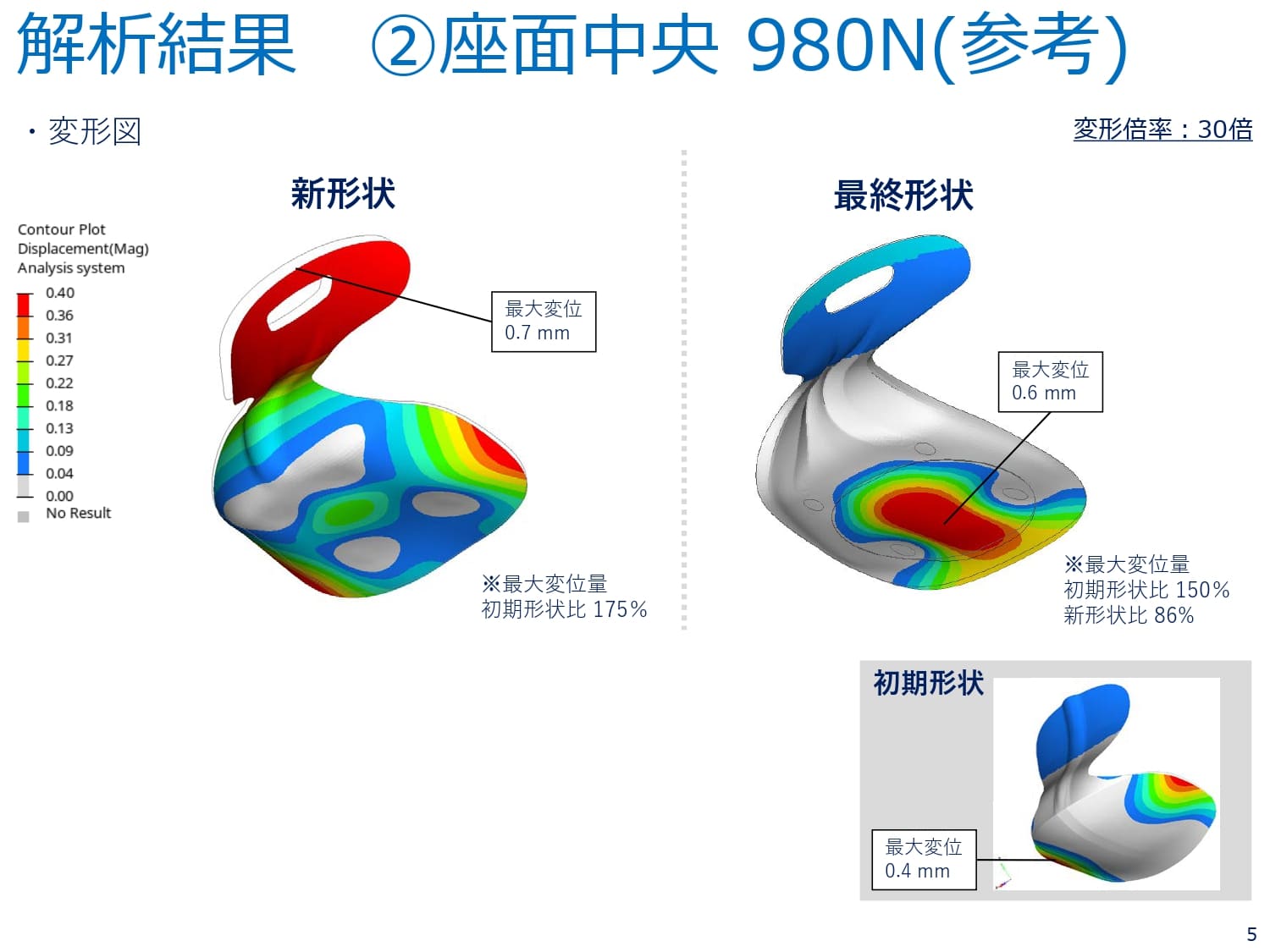
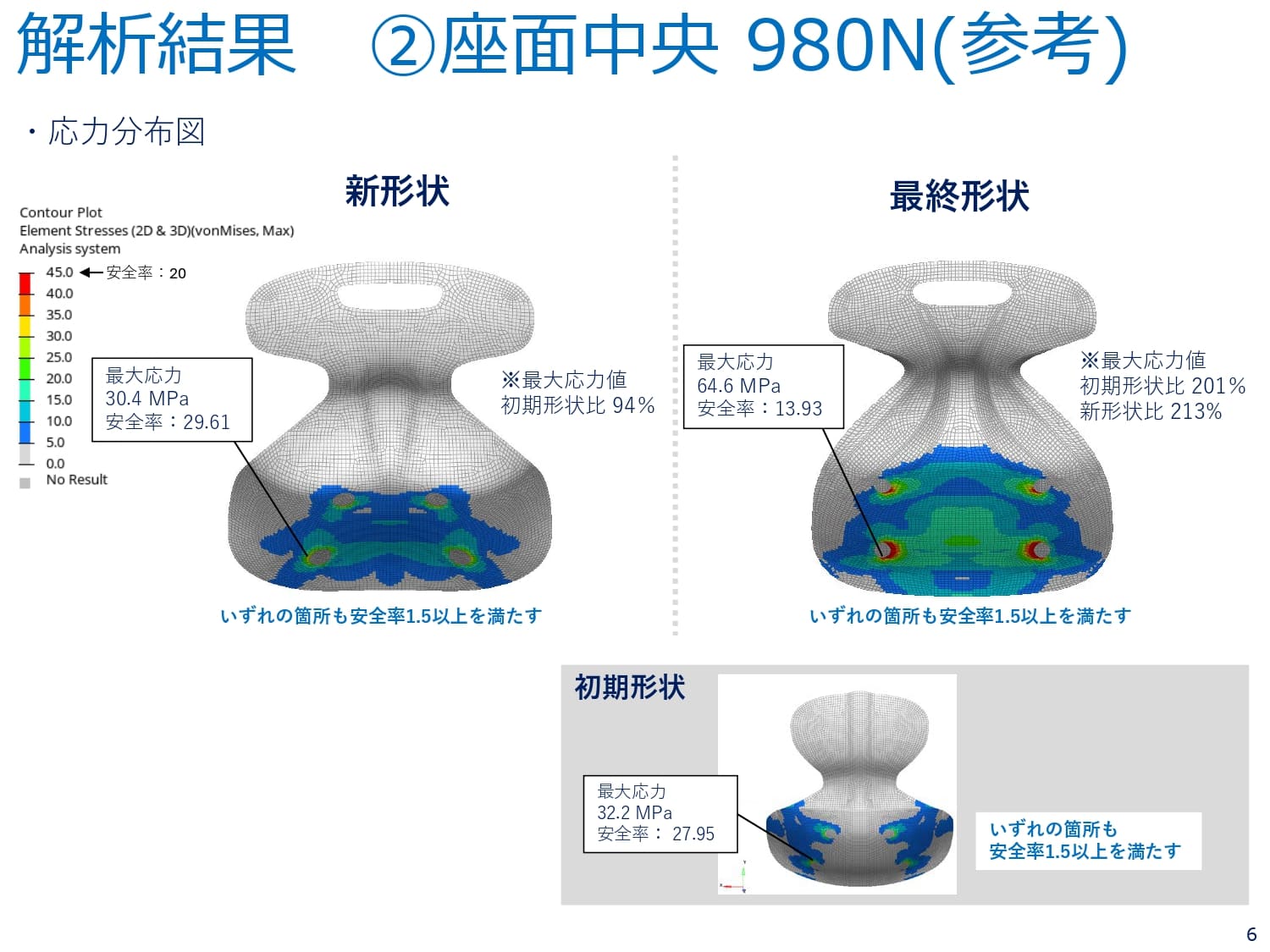
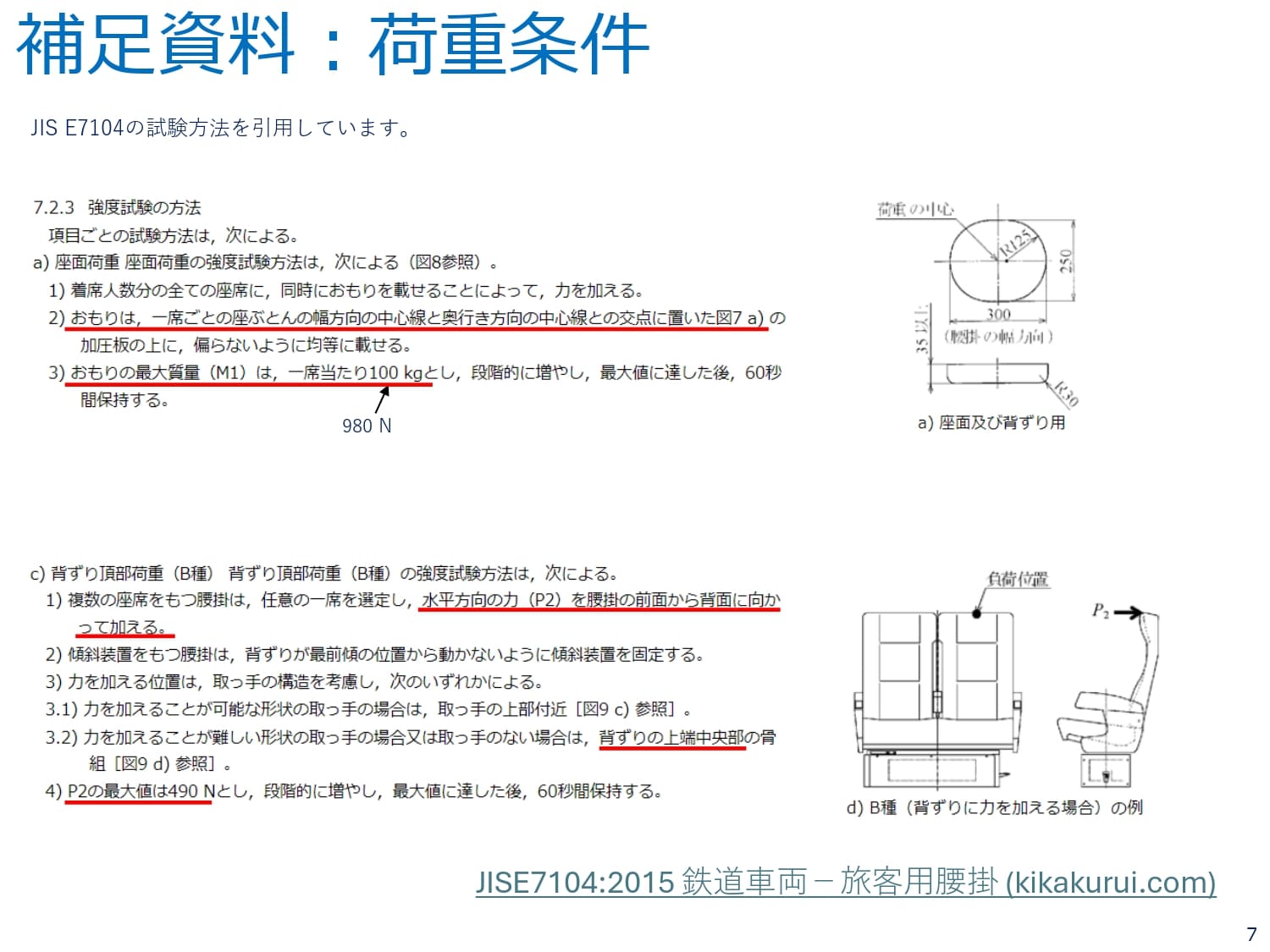
ALL CARBON CHAIR
材質:UD材 / チョップ材 / 不織布材
総重量約1kg・耐荷重約80kgのカーボンで製作した椅子です。
インジェクション製品に比べて製品肉厚を1/3~1/2程度に軽減し軽量化を実現しており、複合材料を用いることで樹脂単体よりも薄く・軽く・高強度の製品となっています。
座椅子部は、姿勢矯正のコンセプトのもと、製品肉厚2mm一定の設定に形状剛性をつけることでクビレと「しなり」を実現し、快適に座れます。
取付座面も座椅子と同時インサート成形(一体成形)し、ボルトナットをインサートし ています。
組付け部品はカーボン3Dプリンターで製作しており、ボルト以外ALL CARBONで製作しています。
脚パイプは、グローブライド様にカーボン曲げパイプをご提供していただきコラボレーションしています。重量は210g程度で鉄の場合1kg程度になるため、約80%の軽量化を実現しています。
carbon+PA 2種類の材料で製品を試作しました。
Ver1 軽量性重視
1kg CFRP不織布 vf30程度(座椅子490g・カーボンパイプ210g・その他320g)★不織布シートを20数枚重ねて2t(1/100程度)に圧縮成形
★vfは低めだが不織布は繊維方向がランダムのため広範囲に粘りのある強度を持たせることが出来る
Ver2 デザイン性重視
1.2kg CFRPチョップ材 vf50程度(座椅子670g・カーボンパイプ210g・その他320g)★材料の流動性が良いため成形性、デザインが良好
★vf50が高めのためUD材でなくても強度が出やすい
プリプレグ(板材)
平板金型で成形した板材、プリプレグです。
CFRP複合材料はロール材や板材・チョップ材など様々な材料がそれぞれのサイズやロットで販売されていますが、製品の成形材料として考えた際 にはちょうど良いサイズが少ないのが現状です。
またプリプレグの厚みや、UD 材とチョップ材などの材料の組み合わせについても成形の都度アレンジする必要があります。
そこで当社ではターゲットとなる製品に対して、適切なプリプレグで成形を可能にするために平板金型を製作しました。これにより 500 角 のプリプレグを 20t まで成形できるようになり、様々なバリエーションを準備できるようになりました。
成形方法はプレス成形です。
プリプレグでお困りでしたらご相談ください。
Facility当社の複合材料成形システム設備のご紹介
当社の複合材料成形システムの設備は、マトリクス樹脂が熱硬化樹脂の複合材料の成形・マトリクス樹脂が熱可塑性樹脂の複合材料の成形において、急温・急冷が可能で、ヒート&クール制御も可能です。
ハイワットヒーターとチラーを組合わせ、32チャンネルに分けて設定することが可能なため、非常に細かな金型温度コントロールを可能にしており、CFRPやGFRPの試作・成形に適した設備です。
そのため、熱硬化性樹脂並びに熱可塑性樹脂の成形を短時間で行うことが可能で、試作リードタイムの短縮を実現します。また、材料加熱装置を併用することで、さらなるサイクルタイムの削減が可能になります。
Material heating device材料加熱装置
複合材料の成形のうちマトリクス樹脂が熱可塑性樹脂である成形において活躍する装置で、当社では「石英管を用いた遠赤外線式材料加熱装置」と「クイックレスポンスヒーターを用いた中赤外線式材料加熱装置」が使用可能です。いずれも成形材料の両面面から加熱することが可能な装置です。
材料加熱装置を用いることで、プレス型での成形において製品形状が深い場合、予め成形材料を加熱して型に設置することで製品形状に沿った材料設置が可能になるため、CFRPやGFRPの成形不良発生を削減できます。
また成形材料が未含浸の材料やセミプリプレグである場合、成形前に予熱を加えることで含浸を補助させます。
さらに、材料を型上で昇温させる場合と比べ成形サイクルの短縮になります。
「遠赤外線式材料加熱装置」は雰囲気温度で材料を加熱するため、じんわり中心部まで加熱することが可能です。
材料板厚の大きい複合材料やサイズの大きい複合材料で使用することをお勧めします。
「中赤外線式材料加熱装置」はセル方式のヒーターを複数組合せることでヒーター1個毎に出力を調整することが可能です。
そのため、部分的にヒーターの出力パターンを制御可能で、製品形状にあった加熱状態にすることが可能です。
また比較的薄い板厚の成形材料が前提になりますが、非常に昇温時間が短く、遠赤外線式に比べ待機時間の削減が可能になります。
加熱材料の中心部分を測定して、ヒーターの温度制御にフィードバックすることが可能で成形材料の温度管理をすることも可能です。
About複合材料とは
複合材料とは、2つ以上の異なる材料を組み合わせた材料のことです。強化のための強化材料と、それを支持するための母材(マトリクス)から構成されています。
複合材料は材料の組み合わせにより、構造などを変えることで、「硬さ・耐久性・重量・靭性・腐食抵抗力」などの性質をコントロールすることが可能になります。
代表的なものに、CFRPやGFRP、FRPなどがあり、様々な分野で注目されています。
Composite material代表的な
複合材料
FRP繊維強化プラスチック
FRP(Fiber Reinforced Plastics)とは、樹脂を繊維で補強することによって、強度剛性を向上させた複合材料です。
FRPには、CFRPやGFRPなどがあります。
FRPはハンドレイアップ成形や、連続成形、SMC成形など、用途に応じて様々な成形方法があります。
CFRP・CFRTP炭素繊維強化プラスチック
CFRP(Carbon Fiber Reinforced Plastics)とは、熱硬化性樹脂または熱可塑性樹脂に炭素繊維を強化材として加えた複合材料です。
軽い樹脂に炭素繊維を加えることで、「軽くて・強くて・腐食しない」という特長を有します。
材料の種類にもよりますが、一般的に鉄材と比べるとCFRPの重量はおよそ1/4程度です。
また、疲労強度に強い、耐薬品性に優れる、通常の熱的環境では安定している、振動減衰特性がある、熱膨張係数が低いといった様々な特性があり、スポーツ用途から産業用途、航空機、自動車に至るまで幅広い用途で使用されています。
引張強度が鉄材の約10倍、非弾性率が約7倍になる材料もあります。
航空機やドローンでは、軽量化と強度の観点から、複合材料でしか成り立たない部品が多いと言われています。
高強度・高弾性である
炭素繊維は鉄の約4倍の引張強度を持ちながら、伸びが非常に少ないという特性を持っています。またマトリクス樹脂より圧縮時の強度が向上します。鉄と同じ質量であれば、強度・弾性率とも大幅にアップする事が出来ます。
軽量材料である
CFRPは高強度・高弾性であり、金属に比べて軽い材料です。炭素繊維の種類やVf(炭素含有率)によって幅がありますがおおよそ1.5~1.7程度の比重です。
設計の自由度が高い
CFRPの材料は材料特性を活かして特定の方向に強く、それ以外の方向に弱い材料を作ることができます。また繊維方向や形状自体、リブ構造などで設計時に強度をコントロールすることが可能です。
耐疲労性がある
CFRPは炭素繊維がハニカム構造でできているため、金属に比べて高い耐疲労性を持ち、長期間の繰返し荷重や振動にも耐えることができます。
振動減衰性
CFRPは樹脂による振動吸収で高い振動減衰性能があります。アルミの約3~4倍、鉄の約10倍の振動減衰率があると言われており、優れた振動抑制効果があります。
熱膨張率が低い
CFRPは基本的に長さ・体積などの熱膨張はほとんど起こりません。そのため精密機器や測定機器など、温度変化による寸法変化が必要とされるものに向いています。
耐熱性を持たせることができる
マトリクス樹脂の種類によって耐熱性は左右されますが、スーパーエンプラといわれる樹脂を使用すれば300℃~400℃程度までの耐熱性を持たせることも可能です。
GFRPガラス繊維強化プラスチック
GFRP(Glass Fiber Reinforced Plastic)とは、ガラス樹脂を、エポキシ樹脂・ポリエステル樹脂・フェノール樹脂・ビニルエステル樹脂等で固めた複合材料です。
プラスチックの弱点である低剛性を改良するために、ガラス繊維と複合することで、物性が強化されています。
FRP(繊維強化樹脂)の中では、比較的安価であるため、最も広く普及しています。
- 金属に比べて軽量(比重は鉄の1/4)で、鉄より強く、アルミより軽い
- 耐薬品性や耐候性、耐食性に優れている
- 形状設計の自由度が高い
といった特徴を有します。
EV車では、他の複合材料製品と組み合わせることで、バッテリーケースのカバーとして使われている実績があります。
主なCFRP・GFRP材料の種類
UD材
一方向のみ繊維をそろえたものをUD(UniDerection)といいます。
金属と異なり異方性であるため、特定の方向に強い材料にすることが可能です。繊維方向に沿った引っ張りや圧縮強度、弾性率は、クロス材の2~3倍になります。強度を表現したい方向に0度、90度、45度、-45度等に組み合わせるなどして、クロスプライ積層で使用します。
また、水平方向に材料を積層すると繊維の特性が大きくなり、垂直方向では樹脂の特性が大きくなるなど、積層の向きにより性能が変わります。通常クロス材よりも安価です。
チョップ材
チョップ材は、UD材をある一定のサイズで細かく裁断した材料です。繊維が分断されているため非常に成形性が良くなります。
また形状起伏が激しい部位やリブ形状などのUD材やクロス材では材料の入りが悪い個所にも対応しやすい材料です。
クロス材(織物)
平織・綾織などの各種織物シートがあります。繊維の折り方によって強度やドレープ性が異なりますが、意匠性を出すことができます。
開繊繊維
開繊とは、丸断面の原糸を幅広く・薄く・均一に広げて開繊糸を製造することです。1K=1,000本の単位で表現されます。一般的にK値が少ないほど製造工数がかかり、品質も良くなるため、高価な開繊繊維になります。
■メリット
薄層化することで樹脂が均一に分散し樹脂含浸性が向上することで機械強度が向上します。軽くて凹凸が少なくなります。層間剥離しにくくなることで疲労強度が向上します。混繊糸(コミングルヤーン)
炭素繊維と樹脂繊維が高次元で均一に分散されており、成形時に樹脂繊維が溶融することで炭素繊維内部から樹脂含浸することで含浸時間が短くなり、かつ成形性が向上します。材料によってはこれまでのCFRTP材料では成形が難しかった複雑形状製品の成形性が飛躍的に向上します。
Matrix resinマトリクス樹脂の種類
複合材料のマトリクス(母材)には合成樹脂が使用されます。その合成樹脂は、「熱可塑性樹脂」と「熱硬化性樹脂」の2種類があります。
さらに熱可塑性樹脂は、「結晶性」と「非結晶性」の2種類に分かれます。
熱可塑性樹脂は、熱を加えると、軟化し、冷却すると硬化します。
一方、熱硬化性樹脂は、熱を加えると硬化します。冷却し再加熱しても硬いままです。
温度変化による
熱可塑性樹脂と
熱硬化性樹脂の違い
結晶性と非結晶性の違い
結晶性 | 非結晶性 | |
---|---|---|
透明性 | 不透明 | 透明な材料も存在する |
硬度 | 比較的硬い (硬度と靱性に優れる) |
比較的柔らかい (靱性に優れる) |
耐熱性 | 高い | 低い |
収縮率 | 大きい (1%以上) | 小さい (1%以下) |
耐溶剤性 | 優れる | 劣る |
熱可塑性樹脂の種類
ポリプロピレン(PP)
ポリプロピレン(PP)は、使用範囲が非常に幅広く最も多く使用されているプラスチック素材の一つです。樹脂の中で最も比重が軽く(0.9程度)、加工性が高い上に、優れた強度を持っており、透明性・発色性も高い特徴があります。
一般家庭で使用されるものとしては例えば、家電製品や文房具、おもちゃやスポーツ用品、オムツ、カーペットや下着などがあります。また工業用としては自動車用のパーツ、医療用注射器の材料や包装フィルム、建設資材では電線ケーブルの被覆にも使用されます。使用形態もさまざまで、単純成形だけでなく速乾性があることから、繊維素材としても使用されています。加工が容易で薄くできるということからフィルムやシートとしても使用されます。
■メリット
・軽量性がある比重が0.9と軽量です。
・耐熱性がある
熱可塑性樹脂のなかでも耐熱温度が高い傾向にあります。
・耐薬品性が高い
薬品による影響を受けにくいため、科学機器や医薬機器などにも多く採用されています。
・機械的強度に優れる
機械的強度に優れており、表面が硬くて耐摩耗性も良好です。
・加工性が良い
切削加工や曲げ加工などの加工がしやすく、射出成形や押出成形などさまざまな製法に対応できます。
■デメリット
・耐候性が悪い紫外線に弱くいため、屋外での使用には適していません。
・接着性が悪い
接着性に乏しい特徴があります。
・印刷性が悪い
そのままだと印刷が難しい材料のため、印刷時には下地処理を施す必要があります。
ポリアミド(ナイロン・アラミド)
ポリアミド(ナイロン・アラミド)は、最も身近なプラスチック素材の一つで衣類の材料として使用されることが多いです。自動車製造に多数使用されており、エンジンカバー、アクセルペダルやドアハンドル、シートベルトなどあらゆる部分に使われています。
ナイロンの使用用途の35%は自動車用といわれています。またその他にもおもちゃ、食品用フィルム、釣り糸や歯ブラシ、衣類やカーペット、ロープなどに使用され、電子機器の基板やコネクタ、ケーブル類、工業用では断熱材や防水シート、配管など、医療用としては手術器具、カテーテルにも使用されています。
*ポリアミドはプラスチックの種類を示すもので、ナイロンはデュポン社が開発したポリアミドの製品名。脂肪族骨格や半芳香族骨格を含むポリアミド。
*アラミドはナイロンの機械的特性をより高めたもので、鋼鉄を超える引っ張り強度や耐熱耐摩耗性を持つものや、高温・耐薬品性がより強化されているものがある。芳香族骨格だけで構成されるポリアミド樹脂。
■メリット
・耐熱性が高いナイロン6.6の融点は265℃、アラミドの融点は320℃と非常に耐熱性に優れているのが特徴です。
・機械的強度がある
特にアラミドは金属の代替品にも用いられるほどの強度があり、他の樹脂やプラスチックよりも強度に優れています。
・耐摩耗性に優れる
表面が硬いため、耐摩耗性に優れています。ナイロンの耐性は、綿の10倍とも言われており、衣料用繊維として代表的な素材となった要因でもあります。
・引張強度に優れる
引っ張り強度や靱性に優れており、特にアラミドは鋼鉄の5倍とも言われております。
■デメリット
・吸水性がある吸水性が高く湿度による性質の変化や寸法安定性の低下が起きるおそれがあります。
・耐候性が低い
紫外線に弱く、屋外での長期間の利用で色落ちや強度の低下などの劣化がおきる恐れがあります。
・帯電しやすい
静電気を発生しやすく帯電が起きます。
PC(ポリカーボネート)
ポリカーボネート(polycarbonate)は、熱可塑性樹脂の一種で、高い透明性や耐衝撃性が特徴のエンジニアリングプラスチックです。
一般用途や工業用途を含め非常に多くの場所で使われている身近な材料で、有機ガラスとも呼ばれます。カメラレンズ、DVD基盤、車のヘッドランプ、スマートフォンのケースとボディ、ヘルメット、看板や高速道路の遮光板、防弾素材など幅広く使われています。
よく似た素材としてアクリルがありますが、ポリカーボネートの方が耐衝撃性や難燃性に勝る一方、加工性やコストにおいてはアクリルの方が優れています。連続耐熱温度は約120℃で、熱変形温度は、130~140℃程度です。
■メリット
・透明性が高い樹脂の中ではトップクラスといわれ、光線透過率がガラス板は92%に対してポリカーボネートは約86%程度あります。携帯電話の前面板等にも使用される程透過率が高いです。
・耐衝撃性が高い
ABSの5倍、塩ビの10倍、アクリルの50倍、ガラスの200倍の耐衝撃性を持っています。
・耐候性が高い
紫外線に強いため、屋外での使用でも劣化しにくいです。また高温・低温に強く(-100℃~140℃と広範囲)、電子レンジや冷凍庫、炎天下でも使用が可能で、他の樹脂よりも劣化しづらいです。
・吸水性が低い
成形収縮率が低いため、寸法精度に優れます。吸水率も低く、寸法安定性も高い素材です。
・加工性が高い
同じ透明樹脂のポリエチレン(PE)やアクリルと比較すると衝撃への強さは約50倍です。また強度がありながらも非常に柔軟な素材で、アルミニウム金属シートと同様に、亀裂や破損をせずに形成することができます。電気絶縁特性が必要な際は、ポリカーボネートが金属の代替材として有効な素材となります。
・自己消火性が高い
難燃剤を添加することでV0グレードにすることが出来ます。
■デメリット
・有機溶剤や界面活性剤に弱い強アルカリ性や有機溶媒に弱く、有機塗料、接着剤等に接触すると劣化・白濁してしまいます。高温高湿度環境下で加水分解が起こりやすくなります。
・傷が付きやすい
応力亀裂を起こしやすく、表面硬度が高くないので、アクリルと比べると傷つきやすいです。
・価格が高め
PET(ポリエチレンテレフタレート)
PET(ポリエチレンテレフタレート)樹脂は熱可塑性樹脂の一種で、高い汎用性を持つ素材のひとつです。構造の似ているPBTとひとくくりでエンジニアリングプラスチックに分類されます。
磁気テープなどにも使われるほか、電子機器部品ハウジング、ディスプレイなどにも使用されます。また、ガラス繊維を混ぜてFRPといわれる繊維強化プラスチックとしても使われるケースも多く、ガラス繊維強化ポリエチレンテレフタレート(GF-PET)は軽くて丈夫な素材として自動車部品などに利用されています。軽量で透明性を持つ素材でありながら、-60℃程度の耐寒性を持つため、食品の包装に適しています。ペットボトルに限らず、卵のパック、フィルムなどさまざまな用途に使用されています。
■メリット
・耐熱・耐寒性がある加工方法に左右されますが、耐熱温度200℃、耐寒温度-60℃程度です。
・加工しやすい
薄いフィルムから厚みのある板状、ペットボトルのような曲線を持つ円柱形と、柔軟に加工できます。
・耐水性がある
PET樹脂は水を通しません。水分による変形などがないことも、液体の容器に使用される理由のひとつです。
・薬品に強い
一部を除き耐薬性があるため、薬品類の包装や医療機器にも使用可能です。
・透明性がある
飲料容器に用いても、飲料の色味を損ないません。
・絶縁性がある
汎用プラスチックに比べて高い電気絶縁性をもちます。
・焼却できる
PET樹脂は塩素を含まないプラスチックであるため焼却してもダイオキシンの発生原因になりません。
・リサイクルできる
PET樹脂から生成された繊維を使用するアパレルブランドも少なくありません。繊維としてはポリエステルとよばれ、合成繊維のうちおよそ30%を占めています。
■デメリット
・強度が弱いエンジニアリングプラスチックとしては強度が弱く、工業用途ではガラス繊維での補強が必要です。
・高温下で加水分解を起こす
高温の水中下のような状況で用いるには困難な素材です。
・耐熱性が低い
PETボトルの耐熱性は50℃程度、耐熱ボトルでも80℃程度です。
・有機溶剤や無機酸に弱い
無機酸に弱く、有機溶剤耐性はアルコール度数20度が目安です。
・耐候性が低い
屋外で使用した場合、劣化する可能性があります。
ABS
ABS樹脂は、アクリロニトリル・ブタジエン・スチレン樹脂ともよばれます。アクリロニトリル、ブタジエン、スチレンという3種類のモノマーで製造されます。
アクリロニトリル:耐熱性、機械的強度(剛性)、耐油性
ブタジエン:耐衝撃性(ゴムの特性)
スチレン:光沢性、成形性(加工性)、寸法安定性
ABS樹脂はさまざまな機械的特徴をバランスよく有しており、見た目も美しいため、汎用的なプラスチック素材として様々な場面で活用されています。自動車用途ではフロントやラジエーターグリル、インストルメントパネル、ドアパネル、フロントカバー、ランプカバー。一般機器や家電としてはテレビ、冷蔵庫、洗濯機、プリンター、複写機、パソコン、電話機、ファックスなどの部品。その他としては玩具・化粧品容器・トイレ・キャリーバック・時計・スポーツ用品・楽器などに使われています。
■メリット
・耐熱温度が高く熱に強い耐熱温度は70~100℃程で、一般的な用途で使用する分には十分だといえます。
・外部からの衝撃に強い
ブタジエンを含むため、ゴムのような耐衝撃性があります。
・用途に合わせて柔軟に加工できる
加工性がよく、射出成形や押出成形、真空成形、3Dプリンターなど様々な方法で成形が可能です。また切削や接着、溶着、めっきや塗装などの表面処理も可能です。
・デザイン性が高い
表面の光沢性や着色性にすぐれているため、製品のデザイン性を高めることが可能です。
・成分を追加または変更して、様々な特性を付与できる
成分を加えたり、既存成分の一部を別の成分と入れ替えたりすることで、様々なABS樹脂をつくり出せます。ガラス繊維を加えて剛性を強化した「強化ABS樹脂」や、ブタジエンのかわりに塩素化ポリエチレンを使用した「ACS樹脂」などがあります。
■デメリット
・耐候性が低く劣化しやすい耐候性が低く、太陽光での紫外線で変色や光沢劣化が起こります。表面加工や紫外線吸収剤の添加などによって耐候性を向上させたABS樹脂もあります。
・有機溶剤に弱い
耐薬品性がそれほど高くないため、有機溶剤によって劣化する場合があります。
・燃えやすい
可燃性の樹脂ですが、難燃剤を加えて燃えにくくしたABS樹脂も存在します。
PEEK
PEEK(ピーク)は熱可塑性樹脂の一種で、プラスチックのなかでも特に高い性能を持った「スーパーエンジニアリングプラスチック(スーパーエンプラ)」に分類される材料です。Poly Ether Ether Ketone(ポリエーテルエーテルケトン)の略称です。
耐熱性、耐薬品性、耐熱水性、難燃性、力学的特性、電気的特性に優れており、医療機器、航空宇宙産業、自動車産業、化学産業、半導体産業など様々な産業分野で使われています。自動車産業ではギア・ベアリングなどの各部品が金属部品の代わりとして軽量化、絶縁性を目的として代替部品として使用されることもあります。
PEEK材は基本グレードの他に、用途に応じて様々なグレードが存在します。
・PEEK強化グレード
カーボン繊維やガラス繊維との複合材料にすることで、通常のPEEKではカバーできない環境下で使われます。繊維材の影響で「ソリ」が発生しやすくなるため、切削加工は難しくなります。
・PEEK導電グレード
一般的にプラスチックには絶縁性能がありますが、PEEKにカーボン繊維を混ぜ込むことで「導電性」を持たせたグレードです。繊維材の影響で切削加工は難しくなります。
・PEEK医療グレード
医療機器の軽量化のために金属代替として使われたり、体内で無毒かつ不活性のため生体適合性を考慮したグレードです。注射針やインプラント、義歯などに活用されています。
・PEEK摺動グレード
部品交換がむずかしい箇所での使用されることが多く、潤滑性・耐摩耗性を向上させたグレードです。炭素繊維やPTFE(四フッ化エチレン)を充填することで耐久性が上がり、機械部品の寿命が向上します。
■メリット
・耐熱性に優れる耐熱性はスーパーエンジニアリングプラスチックの中でも特に優れており、高温環境下で安定した物性を維持できる材料です。連続使用温度は260℃程度、融点は340℃程度です。熱水やスチームに対しても耐性があり、オートクレーブによる高圧蒸気滅菌も可能です。
・機械的特性に優れる
高温環境下でも引張強度や耐衝撃性に優れており、CFやGFを添加することで強度のグレードを上げることもできます。
・耐薬品性に優れる
耐薬品性に非常に優れており、濃硫酸以外の酸やアルカリ性に耐性を持っています。高温環境下でも耐薬品性を有します。
・食品安全性がある
日本の食品衛生法や米国FDAの規格を満たしており、食品接触用途として食品や飲料の加工装置にPEEK製の部品を用いることも可能です。
・難燃性である
燃焼時の発煙や有毒ガスの発生が非常に少ない難燃性の素材です。
■デメリット
・切削加工や切断加工が難しい機械的強度の高い特長を持つことが特徴ですが、それゆえに切削加工や切断加工が難しい材料です。
・コストが高い
1kg当たり約1万円と他の樹脂材料と比べて比較的高価な材料です。この価格は汎用樹脂の約50倍、一般的なエンジニアリング・プラスチックの約30倍程度です。
熱硬化性樹脂の種類
- フェノール樹脂
- メラミン樹脂
- ユリア(尿素)樹脂
- ウレタン樹脂
- エポキシ樹脂
- 不飽和ポリエステル樹脂
- ポリイミド樹脂
- シリコン樹脂
- アルキド樹脂
- ポリアミノビスマレイミド
フェノール樹脂
フェノール樹脂(Phenol Formaldehyde Resin/PF:ポリオキシベンジルメチレングリコールアンハイド ライド)はベークライトとも言われ、フェノール類とアルデヒド類に触媒を加えて付加縮合反応を起こして得る多価メチノールフェノールです。世界で初めて植 物以外の原料から作り出されたプラスチック素材で、熱硬化性樹脂の中で最も生産されている樹脂であり、加熱方法や混合割合により熱硬化、熱可塑の異なる特 性をもつ樹脂を作ることができます。
自動車・鉄鋼関連用としてその優れた耐熱性、耐久性から幅広く使用されており、鉄鋼関連用途では耐火物の製造に使用されています。成形複合製品 では優れた耐熱性・機械的強度を有し、フィルター用、セパレーター用、塗料用、積層用、バインダー用などの様々な含浸用途に使用されています。住宅関連で は環境調和型フェノール樹脂が、環境対応としめ低フリーフェノール型樹脂などもあります。
フェノール樹脂の種類
フェノール樹脂は「ノボラック型」と「レゾール型」という種類に分かれます。ノボラック型とは、酸触媒下で反応させることで得られる熱可塑性樹脂です。
レゾール型とは、アルカリ媒を用いて得られる熱硬化性樹脂です。
■メリット
・電気絶縁性がある・耐熱性を持つ
・断熱性が高い
・難燃性である
・寸法安定性に優れる
・高接着性を持つ
・耐酸性に優れる
・成形性に優れる
■デメリット
・耐アルカリ性に弱い・耐衝撃性が高いわけではない
・毒性があるため分解温度に注意する必要がある
ウレタン樹脂
ウレタン樹脂(PU樹脂/ポリウレタン/Polyurethane)はウレタン結合(イソシアネートとアルコールによって形成されるカーバメー ト結合)によって形成されるポリマーの総称です。使用するポリイソシアネートとポリオールの性質によってさまざまな物性のポリウレタンを合成することが可能で、軟らかいものから硬いものまで様々な種類が存在し、接着性や耐摩耗性に優れおり、発泡体としても活用されています。熱可塑性、熱硬化性の双方の性質 を得ることが可能です。
ウレタンは発泡体の場合であればクッション、自動車などのシート、断熱材、スポンジ類、コーキング材として用いられます。非発泡体であれば、パッキン・ベルト、塗料、防水材に用いられます。
■メリット
・耐油性に優れる・耐薬品性が高い
・耐久性が高い
・クッション性に優れる
・機械的強度に優れる
・低温特性がある
・耐摩耗性がある
・耐侯性がある
■デメリット
・耐熱性が低い・耐水性が弱い
エポキシ樹脂
エポキシ樹脂は、エンジニアリングプラスチックに分類される熱硬化性樹脂です。単体の反応ではなく、様々な硬化剤と混ぜることで反応します。硬化剤の種類や量によって様々な物性に変化し、様々な特性を引き出すことができます。副産物を出さない特徴があります。
エポキシ樹脂はその硬化特性から接着剤や塗料としての用途で使用され、高い電気絶縁性・耐水性・耐食性によりコーティング剤や建築素材、接着剤 などとしても使用されます。その活躍の場はエレクトロニクス、食品、船舶、航空宇宙産業、スポーツ用品、複合材料としてや3Dプリンター用材料など多岐に渡ります。
■メリット
・耐水性が高い・耐腐食性に優れる
・耐熱性が高い
・耐薬品性に優れる
・耐湿性に優れる
・耐候性が高い
・絶縁性に優れる
・接着性に優れる
・柔軟性がある(性質変化が多様)
・寸法安定性に優れる
・機械強度が高い
■デメリット
・紫外線により劣化する・低温下では固まるまでに時間を要する
・靭性は高くない
不飽和ポリエステル樹脂
ポリエステルとは、エステル結合を持つ高分子化合物です。そのポリエステルには2種類あり、1つは飽和ポリエステル、もう1つ は不飽和ポリエステルです。
飽和ポリエステルは、熱可塑性・無反応性・不飽和酸を含まないなどの特徴を持っており、PBT・PET・飽和ポリエステル・アルキッドなどがあります。不飽和ポリエステルは、スチレンに代表される架橋性モノマーに溶解した熱硬化性樹脂です。
ガラス繊維や炭素繊維等の強化繊維で強化したFRP(Fiber Reinforced Plastics)用途と、注型・塗料等の繊維強化せずに使用する非FRP用途があります。
常温硬化には、過酸化物触媒と促進剤の併用される。加熱硬化は、中温硬化系と高温硬化系に分けることができます。
■不飽和ポリエステル樹脂の用途
・樹脂の粘度が低く、強化繊維への含浸性に優れる。種々な成形方法に対応可能。・硬化時に揮発性の副生成物が無い ・硬化後は機械 的性質、電気的性質、耐水性、耐熱性、耐薬品性に優れる
・耐薬品性に関して、酸に強いですが、アルカリに弱い
・電気的特性に優れており、塗料や接着剤に使用される
・常用できる耐熱温度は130~150℃、比重は1.1から1.4といわれる
・成形収縮率が低い
・寸法安定性が高い
・低圧力で成形でき、成形性が非常に良い
■不飽和ポリエステル樹脂を用いた成形材料
・SMC (Sheet Molding Compound)不飽和ポリエステル樹脂に各種充填材と添加剤を配合した樹脂ペーストに、所定の長さにカットしたガラス繊維を含浸させた成形材料でシート材料で、圧縮成形が可能。材料製造時にも成形時にもガラス繊維の損傷を受けないため成形品の強度が高くなります。
・BMC (Bulk Molding Compound)
不飽和ポリエステル樹脂に各種充填材や添加剤を配合し、ガラス繊維を混練機にて含浸させた成形材料で塊形状であり、インジェクション成形・トランスファー成形・圧縮成形が可能です。材料製造時の混錬と成形時の成形機内における混錬によってガラス繊維を損傷するが寸法精度が高くなります。
シリコン樹脂
シリコンとはケイ素(Si)のことを指す言葉です。ケイ素とは元素の一種で、地球上では酸素に次いで多く、自然界や体内のあらゆるところに存在します。
シリコン樹脂はこのケイ素を原料とした樹脂化合物です。シリコンはケイ素であり、シリコン樹脂はシリコンを原料とした化合物です。
■メリット
・安全性が高い人体に無害で用途の幅が広く、食品衛生法による適合品としても認められています。
・耐熱性と耐寒性が高い
250℃までの高温や-60℃の低温にも耐えることができます。
・電気絶縁性が高い
電子部品などで多用されています。
・表面張力が高く、撥水性・消泡性・離型性(非粘着性)に優れる
多くの素材にくっつかない特性を持つが、ガラスにはくっつきやすい性質を持ちます。
・耐候性が高い
酸素やオゾン、紫外線などに対する高い特性を持つため屋外でも利用できます。
・耐薬品性・耐溶剤性に優れる
劇薬や有毒物質にも強い特性があります。
・耐油性は100℃以上の環境のみ高くなる
・熱伝導率が低い
・高い撥水性を持つ
・化学反応性が低い
■デメリット
・引張り強さや引き裂き強さなどの強度が低い・耐磨耗性が低い
Company会社概要
- 社名
- 応原工業株式会社
- 代表者
- 代表取締役社長 應原 弘圭
- 所在地
- 〒739-0153
広島県東広島市吉川工業団地8-11 - 電話番号
- 082-429-0553(代)
- FAX
- 082-429-0417
- 設立年月
- 1967年(昭和42年)8月
- 資本金
- 2,080万円
- 従業員
- 20名(2023年9月現在)
- 事業内容