About複合材料とは
複合材料とは、2つ以上の異なる材料を組み合わせた材料のことです。強化のための強化材料と、それを支持するための母材(マトリクス)から構成されています。
複合材料は材料の組み合わせにより、構造などを変えることで、「硬さ・耐久性・重量・靭性・腐食抵抗力」などの性質をコントロールすることが可能になります。
代表的なものに、CFRPやGFRP、FRPなどがあり、様々な分野で注目されています。
Features応原工業の複合材料の
試作・金型製作の特徴
特徴1創業50年以上
金型設計・製作の
高い技術力
当社は、創業以来50年以上、自動車部品の樹脂プレス金型の設計・製作を行ってまいりました。長年培ってきた技術力への評価をいただいており、本社のある広島県のみならず、全国各地のお客様と取引をさせていただています。
この技術で、複合材料の金型も高精度に加工し、複合材料の試作を行います。万が一、製品に不具合が発生した場合でも、金型から対応しているため、すぐに解決いたします。
また、当社の複合材料成形システムは、カスケード制御により、形状面に近い箇所も温度管理しています。これにより、適正な成形温度を維持でき、理想的な成形条件にすることが可能です。
当社では、これまでプレス成形では難しかった複雑形状やリブ形状、また複数の材料を同時に成形することで製品物性・温度・重量・コスト・形状やデザインといったお客様の課題解決をご支援します。
特徴2数個程度の試作から対応
ロットに応じた
コストダウンも可能
当社では、複合材料の成形について、数個程度の試作から対応いたします。
また、金型に関する長年の知見を活かし、ロットに応じて最適な金型の鋼材を選定することが可能です。
これにより、コストの最適化を実現します。
特徴3複合材料成形システムを用いた金型では最大製品サイズ
600×800 まで対応
当社の複合材料成形システムを用いた場合、金型サイズは最大 800×1,000 まで、製品サイズですと最大 600×800 まで対応可能ですので小型のワークだけでなく、大型のワークにも対応可能です。
*ご予算や成形サイクルの条件がマッチすればそれ以上のサイズも可能です。
本社のある広島県のみならず、西日本また、全国の様々な企業に納品可能です。
特徴4熱硬化性樹脂の成形なら最大型サイズ
1,550×2,000 まで対応可能
当社では自動車内装用金型を手掛けておりますので、既存設備を活用すると型サイズ1,550×2,000 まで対応が可能です。
その場合ヒート&クールはできませんが、成形温度は 260℃まで対応可能です。
主に自動車業界向けの実績が多数ございます。
大型の熱硬化性樹脂をマトリクスとした複合材料の成形をお考えでしたらご相談ください。
特徴5製品サイズに応じた
材料をアレンジ
□500までのプリプレグ、
板材の成形が可能
従来は、複合材料を購入するとなると、大板で購入する必要があったため、製品サイズに比べて大きい場合が多く、コスト増につながっていました。
また、材料メーカーの規格品がなければ、連続繊維/プリプレグ(樹脂があらかじめ予備含侵された炭素繊維シート)を用意することができませんでした。
当社ではプリプレグ成形用金型を内製しているため、連続繊維/プリプレグのVF率調整も可能です。
また、材料厚みは20tまでの板材が成形可能で、UD材・チョップ材・不織布などを組み合わせることでお好みのプリプレグや板材の製作が可能です。
特徴6成形材料のアレンジや、
リサイクル材に対応
当社では、成形材料のアレンジも対応可能です。材料に応じた最適な金型製作・製品試作を行います。
また、一般的に複合材料はリサイクルが難しいと言われていますが、最近は技術開発が進み、新品よりも価格の低いリサイクル材もあります。
環境にも優しいため、多くのご相談をいただいております。
お気軽にお問い合わせください。
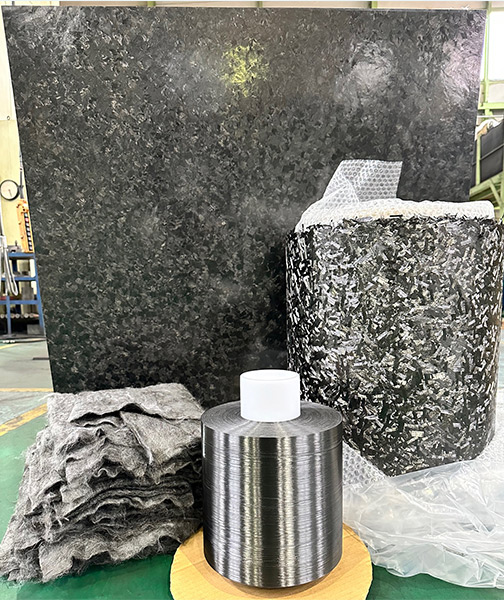
Works製品事例
EVのバッテリーカバー部品
材質:マイカ
こちらは、EVのバッテリーカバー部品です。
ある材料メーカーから自動車部品に参入したいとのことでご相談をいただき、金型を製作いたしました。
バッテリーが発火しないように、「マイカ」という絶縁性の材質を使用しています。試作型を製作し、検証を行い問題がなかったので、試作を行い、納品いたしました。
今回のケースでは、試作型の製作開始から約1年で量産に至りました。
ドローンアーム(ハット形状・リブ形状)
材質:UD 材+チョップ材 / クロス材+チョップ材 / 不織布材+チョップ 材 / 不織布材 / チョップ材
ドローンは長時間・長距離を飛ぶ必要があり、荷物や農薬などを運ぶために軽量化が求められます。そのためドローン部品には、金属より軽く、金属相当の強度のある複合材料がよく使われます。
こちらのワークは、先端の穴にブレード(羽)を取り付けるドローンアームの試作品です。
表側はクビレ形状と製品の高低差があるため、成形性と温度管理が難しいワークです。
裏側は強度を持たせるためのリブのイメージと、ハチの巣形状で金属では成形できない形状を表現しています。
成形方法はプレス成形で1ショットで成形しました。
自動車エンジンルームの補強部品(リブ形状)
材質:UD材+チョップ材 / チョップ材
自動車のエンジンルーム内の板金部品を CFRP に置き換えた 1/2 イメージの部品です。
現在の自動車のトレンドである EV 車はバッテリー重量が重いため、車体重量が内燃機関の車に比べて重くなりますが、部品の素材を金属か ら CFRP に変更することで車体重量の軽量化が可能になります。
こちらの部品は製品形状をあえて複雑化し、金属では実現できないリブ構造にすることで部品の強度向上を実現しています。リブは 1mm で 深さは 23mm です。全て MC による切削加工です。
表側は UD 材を用いることでその繊維方向に対する強度が強くなり、それだけでは弱い方向や捻り方向の強度を向上させています。
成形方法はプレス成形です。
複合材料は材料費が高額なため今回、部品を成形する前に当社の 3D プリンターで出力し、形状の現物確認を行いました。3D プリンターは成形可能サイズが A4 サイズですので 3 分割し、張り合わせることで 1/1 スケールのモデルに仕上げました。
材料特性は全く違いますが、実際の形状にすることで形状的な強さ弱さを知るヒントになります。
座椅子(深絞り形状)
材質:UD材+チョップ材 / チョップ材 / クロス材
床・椅子ともに使用可能な座椅子製品です。
非常に深絞り形状ですが、当社の樹脂プレス金型の製作実績を活かして金型を製作しました。
一般的な成形方法であるインジェクション(射出成型)では座椅子製品の製品肉厚4~6tほどの製品ありますが今回、CFRP複合材料の特性である軽量化と強度を活かして全面2tの製品を成形しました。
また腰の部分は「しなり」が入り、快適に座れるようになっていますが、CFRP複合材料のUD材の強度や形状剛性を持たせることで細い面での「しなり」を実現しています。
成形方法はプレス成形で1ショットで成形しました。
プリプレグ(板材)
平板金型で成形した板材、プリプレグです。
複合材料はロール材や板材・チョップ材など様々な材料がそれぞれのサイズやロットで販売されていますが、製品の成形材料として考えた際 にはちょうど良いサイズが少ないのが現状です。
またプリプレグの厚みや、UD 材とチョップ材などの材料の組み合わせについても成形の都度アレンジする必要があります。
そこで当社ではターゲットとなる製品に対して、適切なプリプレグで成形を可能にするために平板金型を製作しました。これにより 500 角 のプリプレグを 20t まで成形できるようになり、様々なバリエーションを準備できるようになりました。
成形方法はプレス成形です。
プリプレグでお困りでしたらご相談ください。
Facility当社の複合材料成形システム
設備のご紹介
当社の複合材料成形システムの設備は、単純な熱硬化・熱可塑対応だけでなく、急温・急冷が可能でさらに、ヒート&クール制御が可能です。
そのため、熱硬化性樹脂の成形や、熱可塑性樹脂の成形が短時間ででき、試作リードタイムの短縮を実現します。
また、材料加熱炉を使用することで、さらなるサイクルタイムの削減が可能になります。
Material heating device材料加熱装置
複合材料の成形のうち、主にマトリクス樹脂が熱可塑性樹脂である成形において活躍する装置です。
プレス型での成形において製品形状が深い場合、予め成形材料を加熱して型に設置することで製品形状に沿った材料設置が可能になるため、不良の発生を削減できます。
また成形材料が未含浸の材料やセミプリプレグである場合、成形前に予熱を加えることで含浸を補助させます。
さらに、材料を型上で昇温させる場合と比べ成形サイクルの短縮になります。
Matrix resinマトリクス樹脂の種類
複合材料のマトリクス(母材)には合成樹脂が使用されます。その合成樹脂は、「熱可塑性樹脂」と「熱硬化性樹脂」の2種類があります。
さらに熱可塑性樹脂は、「結晶性」と「非結晶性」の2種類に分かれます。
熱可塑性樹脂は、熱を加えると、軟化し、冷却すると硬化します。
一方、熱硬化性樹脂は、熱を加えると硬化します。冷却し再加熱しても硬いままです。
温度変化による
熱可塑性樹脂と
熱硬化性樹脂の違い
結晶性と非結晶性の違い
結晶性 | 非結晶性 | |
---|---|---|
透明性 | 不透明 | 透明な材料も存在する |
硬度 | 比較的硬い (硬度と靱性に優れる) |
比較的柔らかい (靱性に優れる) |
耐熱性 | 高い | 低い |
収縮率 | 大きい (1%以上) | 小さい (1%以下) |
耐溶剤性 | 優れる | 劣る |
熱可塑性樹脂の種類
熱硬化性樹脂の種類
- フェノール樹脂
- メラミン樹脂
- ユリア(尿素)樹脂
- ウレタン樹脂
- エポキシ樹脂
- 不飽和ポリエステル樹脂
- ポリイミド樹脂
- シリコン樹脂
- アルキド樹脂
- ポリアミノビスマレイミド
Composite material代表的な
複合材料
FRP繊維強化プラスチック
FRP(Fiber Reinforced Plastics)とは、樹脂を繊維で補強することによって、強度剛性を向上させた複合材料です。
FRPには、CFRPやGFRPなどがあります。
FRPはハンドレイアップ成形や、連続成形、SMC成形など、用途に応じて様々な成形方法があります。
CFRP・CFRTP炭素繊維強化プラスチック
CFRP(Carbon Fiber Reinforced Plastics)とは、熱硬化性樹脂または熱可塑性樹脂に炭素繊維を強化材として加えた複合材料です。
軽い樹脂に炭素繊維を加えることで、「軽くて・強くて・腐食しない」という特長を有します。
材料の種類にもよりますが、一般的に鉄材と比べるとCFRPの重量はおよそ1/4程度です。
また、疲労強度に強い、耐薬品性に優れる、通常の熱的環境では安定している、振動減衰特性がある、熱膨張係数が低いといった様々な特性があり、スポーツ用途から産業用途、航空機、自動車に至るまで幅広い用途で使用されています。
引張強度が鉄材の約10倍、非弾性率が約7倍になる材料もあります。
航空機やドローンでは、軽量化と強度の観点から、複合材料でしか成り立たない部品が多いと言われています。
GFRPガラス繊維強化プラスチック
GFRP(Glass Fiber Reinforced Plastic)とは、ガラス樹脂を、エポキシ樹脂・ポリエステル樹脂・フェノール樹脂・ビニルエステル樹脂等で固めた複合材料です。
プラスチックの弱点である低剛性を改良するために、ガラス繊維と複合することで、物性が強化されています。
FRP(繊維強化樹脂)の中では、比較的安価であるため、最も広く普及しています。
- 金属に比べて軽量(比重は鉄の1/4)で、鉄より強く、アルミより軽い
- 耐薬品性や耐候性、耐食性に優れている
- 形状設計の自由度が高い
といった特徴を有します。
EV車では、他の複合材料製品と組み合わせることで、バッテリーケースのカバーとして使われている実績があります。
Company会社概要
- 社名
- 応原工業株式会社
- 代表者
- 代表取締役社長 應原 弘圭
- 所在地
- 〒739-0153
広島県東広島市吉川工業団地8-11 - 電話番号
- 082-429-0553(代)
- FAX
- 082-429-0417
- 設立年月
- 1967年(昭和42年)8月
- 資本金
- 2,080万円
- 従業員
- 20名(2023年9月現在)
- 事業内容